When we built a new shop, we set out to up our game. And then we said to ourselves, let’s not just up our game, let’s go for best in class.
FAQs
What the hell is a timber frame, anyway?
Answering the question everybody is afraid to ask: “What the hell is a timber frame, anyway?”
Carolina Timberworks Timber Frame Construction Process
or… What to Expect When You’re Expecting a Timber Frame
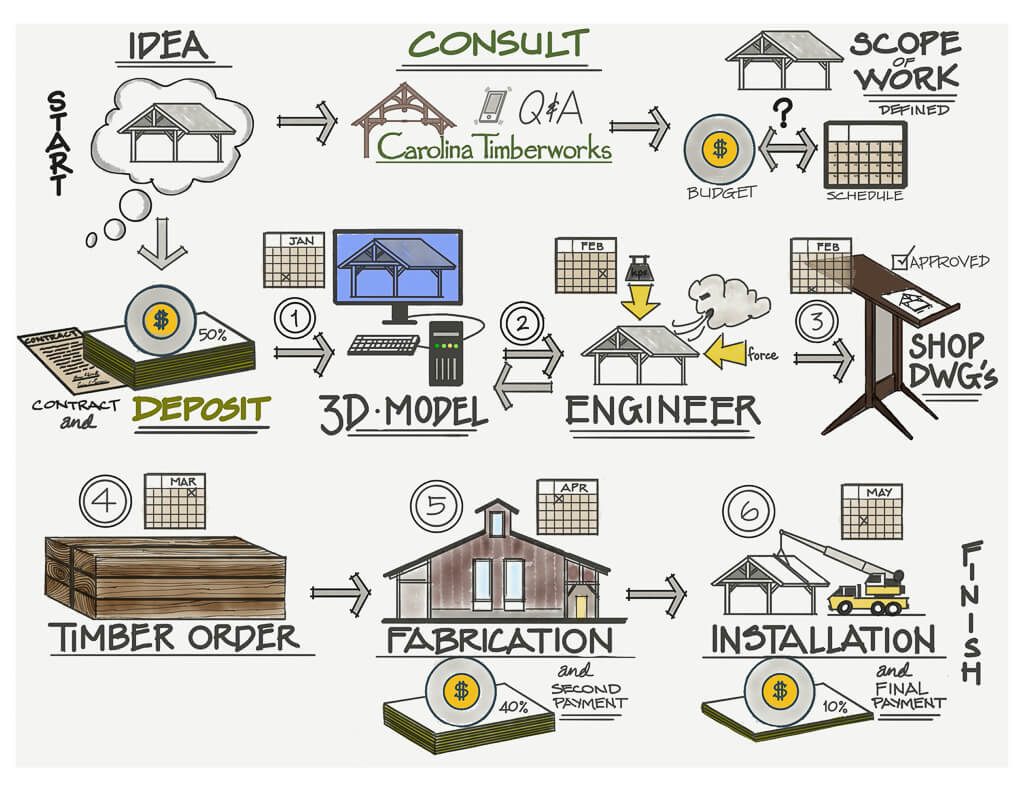
The timber frame construction process is important, regardless of how well the finished product turns out—just ask someone who endured a terrible process to obtain their timber frame.
There is neither a shortcut, nor any secret to designing a timber frame. But whether good or bad, every timber frame company has a process. This is ours.
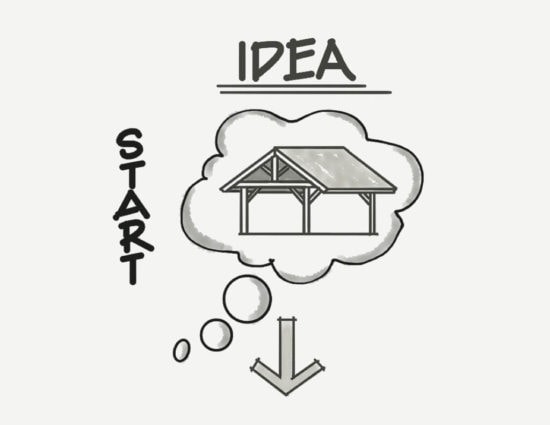
It starts with a dream: a spark that inspires a homeowner or a business owner to build something.
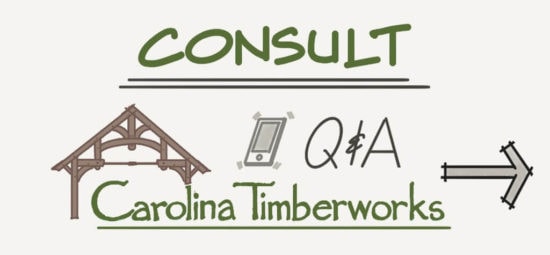
We’ve been doing this long enough to know that we’re not the right fit for every project that comes along. We half-jokingly call this first meeting the “dating phase.” There’s an understood agreement that this meeting is about learning about one another—how we both like to work, what makes us tick, our expectations. We ask you questions, and we answer your questions. (Here are some good ones: How to Interview a Timber Frame Company). Afterward, if either of us doesn’t think the partnership is a good fit, we say so, parting ways amicably and with no hard feelings—and with no expectation of a second date.

But if, on the other hand, we both agree the match has potential, the discussion turns to taking the budding relationship to the next level. The rosy flush of romance may fade considerably at this point because we (Carolina Timberworks) will bring up the subject of money on only the second date. Tacky, right? To make matters worse, we’ll throw in questions about timing. Uncomfortable though it may be, this refreshingly open communication results in saving both of us a lot of time, money, and frustration. After all, you probably don’t want to spend months waiting (and paying) for a timber frame design, that when finally priced, turns out not to fit your budget.

At this point, it’s time to talk commitment. You’re about to “marry” a timber framer—something your mother probably warned you about. (Okay, maybe not. But bet you didn’t know that timber framers’ mothers warn them about marrying the wrong clients!) Doubt and fear make their appearances. But this is why prenuptial agreements (contracts) were invented. Really good timber frame contracts are all about reducing future disagreements and problems by carefully defining what success looks like. The best ones are easy to understand, fair to both parties, contain good drawings, and are typically fairly lengthy. You wouldn’t sign a one-page prenuptial agreement, would you?
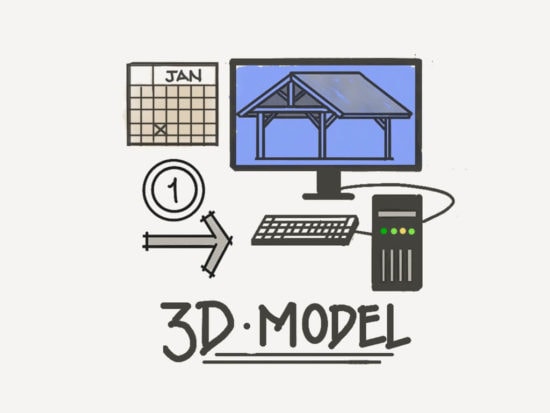
Now something weird happens in the relationship: At this point your honeymoon begins, but your timber framer has to go to work. While you’re basking in the sense of accomplishment that comes from knowing that you’ve conceived the latest addition to your family, your timber framer will be spending a great many days/evenings/weekends in front of a monitor, painstakingly working out a whole lot of details.
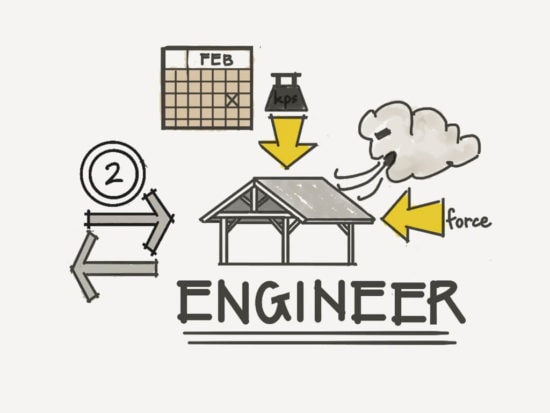
It’s three weeks into your honeymoon. You feel a bit guilty about emailing your timber framer that breathtaking photograph of your view of the Matterhorn from the Mont Cervin hotel in Zermatt, Switzerland. Hard at work, your timber frame spouse replies rather distractedly and with some frustration: “The engineer just called. He woke up in the middle of the night worried about…” The words every timber framer dreads. The “separate honeymoon” phase continues.
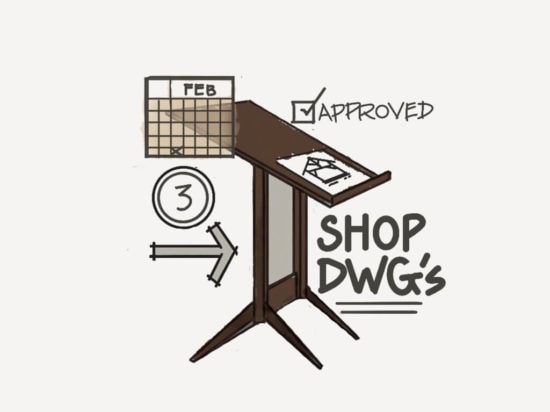
If children were produced like timber frames, sometime prior to birth, you’d receive, with a certain amount of fanfare, an amazingly complex set of drawings from the doctor with every measurement of your baby you could want—and quite a few more—including views from every possible direction or angle. To your dismay, you realize the timber frame shop drawings are pretty complex, and out of your realm of knowledge of design. It’s at this point your architect, builder, or contractor steps in with their trusty red pen, marking up the drawings and suggesting changes. Back to the timber frame shop the drawings go to the love of your life (your timber framer), and in due course, a revised set of drawings arrives in your inbox. Upon consultation with your architect or builder, one of you will sign off on the shop drawings, thereby unleashing the timber frame dogs of war (okay, that doesn’t really work, but always wanted to work that phrase in somewhere).
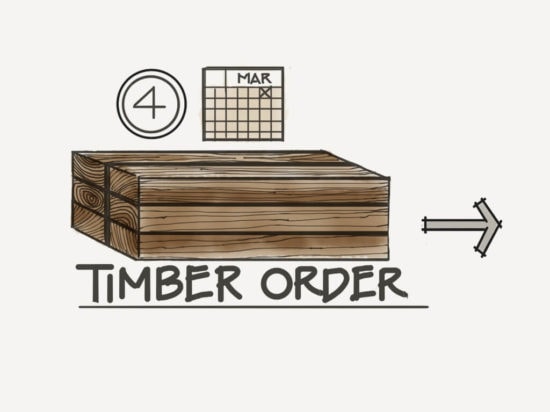
The timber procurement process is a bit like gestating a baby: there are times where it seems like not much is happening. This can be a blessing, for your often hyper-focused timber frame mate appears to relax a bit, and even suggests a meeting. The subject? What to Expect When You’re Expecting a Timber Frame— The Next Steps.
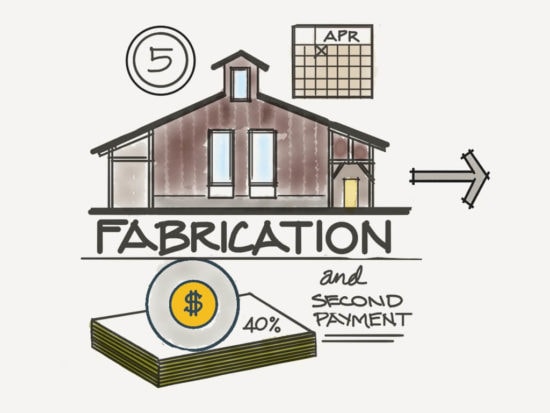
The first thing most people do when walking into a timber frame shop is to pause, smile, and comment how good it smells. Just like babies, freshly cut timber smells good! And just as babies symbolize new life, the beginning of a new job in a timber frame shop always feels like a fresh new start. Some timber frame parents just can’t wait for a peek at their new child, and visit the shop for an early “reveal”. Others, preferring to be surprised, are willing to wait just a few more weeks…
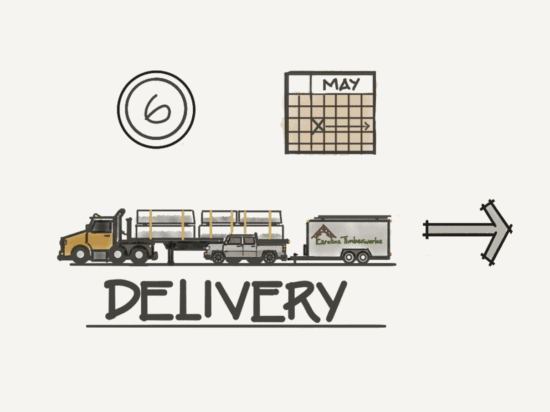

Suddenly, after months and months of slowness, things start to happen—fast. You’ll know you’re entering the final phase when your timber frame spouse’s extended family starts arriving in their pickups to raise your timber frame. You knew the “relatives” (our crew) was part of the deal, but you never expected this many beards, that they’d be this hungry, or that they’d be this nice!

Here’s another family secret: Timber framers don’t really like clothes. Don’t believe me? Watch carefully. Once the timber frame is standing, the crew’s phones will come out. And if you’re lucky you’ll catch a glimpse of each member of the crew, your extended family now, casting one last glance at their baby just before they depart. And if you could read their thoughts, you’d know they think the baby will never look more beautiful than at this moment—completely naked, without a stitch of siding, roofing, or other finishing touch.

Mass Timber Construction: Why Is It Important?
Did you know that mid-rise and high-rise buildings can now be built out of wood? Mass timber is quickly gaining momentum as a viable alternative to traditional construction methods.
What is mass timber? What is mass timber made of?
Mass timber is an emerging building typology that replaces steel, masonry, and concrete with wood. With mass timber, architects and engineers can pursue sustainable construction, warmer aesthetics, and remarkable improvements in construction efficiency.
Although mass timber is a relatively new category, it already features a wide variety of products. Below, we’ll cover nail-laminated timber, glued-laminated timber, dowel-laminated timber, and the mass timber product gaining the most traction: cross-laminated timber.
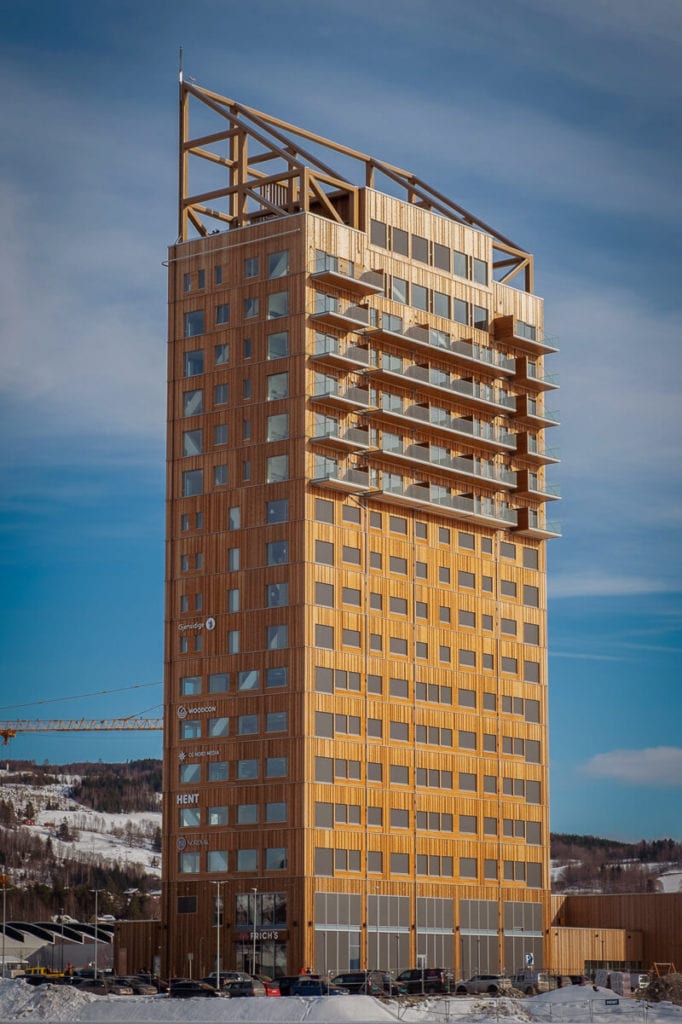
What’s the big deal with mass timber?
Because of the potential to significantly reduce carbon emissions in the atmosphere and reverse climate change, these benefits are plausible due to two key facts about construction:
- First, carbon emissions from the building industry account for approximately 40% of global carbon emissions.
- Second, the manufacture of concrete and steel contributes about 10% of current global carbon emissions.
Andrew Ruff of Connecticut-based Gray Organschi Architecture explains, “If you look 30 years down the road to 2050, we’re projected to have 2.3 billion new urban dwellers. That is a huge amount of construction. Every day that goes by that we don’t convert from mineral-based extractive construction techniques to carbon sequestering building systems, we tend to dig ourselves further in a hole” (Yale Environment 360: As Mass Timber Takes Off, How Green is this New Building Material?, April 2019).
Conversely, using wood in mass timber building actually removes carbon dioxide (CO2) from the atmosphere. Scientists refer to the process as carbon sequestration, but we like to think of wood as a carbon sponge. A tree is nature’s solar-powered CO2 storage machine, until the day it dies. Then, if left to rot—whether in a forest or landfill, or the wood burned—the sponge is wrung out and the CO2 returned to the atmosphere.
Here’s where it gets interesting: take that same wood and keep it dry, as part of a building in the form of mass timber—whether a timber frame, glulam trusses, or cross-laminated timber walls and floors—and it will last indefinitely. Hundreds of years. Longer than concrete.
Mass timber is part of the solution to our climate change problem.
What to Know About Mass Timber
The term mass timber might be confusing to some of us. First things first – a mass timber definition: the term mass timber refers to a building typology—a way in which the building itself is made of large, solid wood structural pieces for wall, floor, and roof construction.
What is Mass Timber Made Of?
As large solid pieces of timber become more expensive to source, mass timber is being fabricated using many smaller individual pieces of wood—literally tons of wood go into the making of these manufactured structural pieces. With mass timber, the large engineered wood structures of a building are made entirely of wood—usually the beams, columns, arches, floors and roofs—and fabricated offsite to engineered specifications.
Hence, the term mass refers to the large, solid components, and the term timber refers to a solid or manufactured wood product.
What is a Mass Timber Building?
One more thing that might help – the criterion to define a mass timber building is as follows: If the primary load-bearing structure is made of either engineered or solid wood, we can call it a mass-timber building. If the building uses mass timber as an accent and not as a primary structural element, then it is not mass timber. (Construction Dive: Mass Timber 101: Understanding the Emerging Building, May 2017)
Advantages of Mass Timber
- Faster and Cheaper Construction: Because mass timber is fabricated and sometimes even assembled offsite, it allows for a more efficient and more cost-effective construction process.
- Improved Fire and Earthquake Safety: In contrast to stick-built structures, mass timber buildings are more fire resistant—largely due to the larger, heavier, and more compressed timber.
- Reduced Emissions: Steel and concrete are highly embodied building materials—meaning they produce a tremendous amount of carbon emissions. Mass timber is made from wood, which is a carbon sink and a renewable resource.
Types of Mass Timber Systems
- Post and Beam: With its vertical posts and horizontal beams, post and beam construction is ideal for buildings with open interior spaces. Although it’s related to timber framing, post and beam uses metal connectors and fasteners.
- Floor and Wall: Mass timber can completely replace steel and concrete to form floors and walls of mid- and high-rise buildings. Floor and wall systems often use a honeycomb structure to manage vertical and lateral loads.
- Hybrid Systems: In addition to timber, hybrid systems include materials like concrete and steel. With hybrid systems, you can choose the best material for the job while still enjoying the benefits of mass timber.
What are the most common timber products?
Sawn Solid Timber (timber framing, post & beam construction)
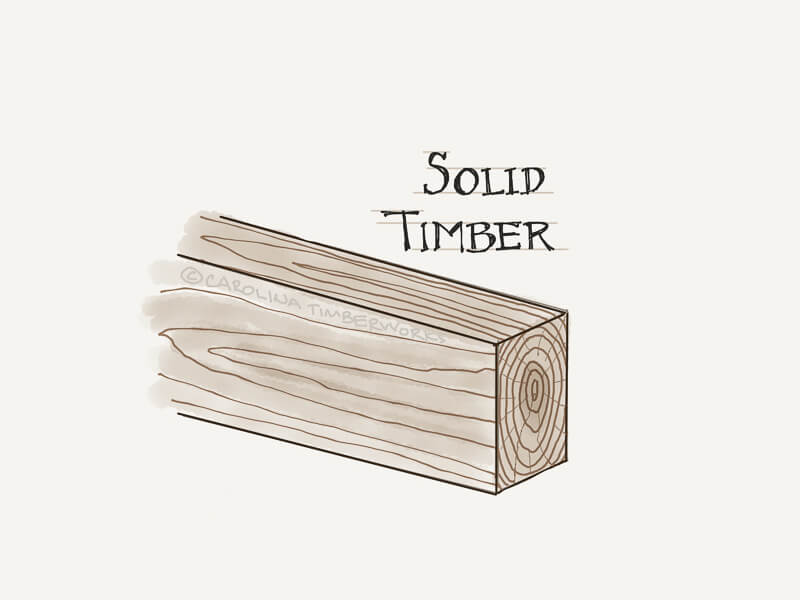
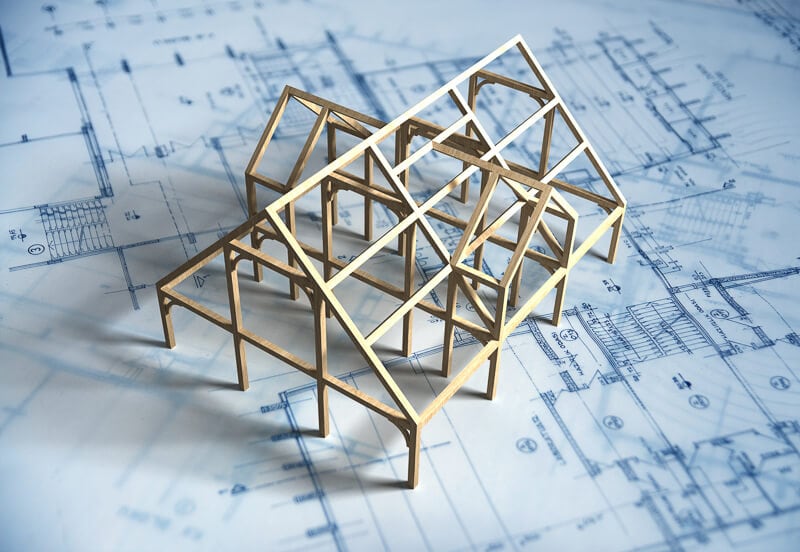
Traditional timber framing is the more than 2,000 year old building method (some would argue it’s an art) of connecting two or more pieces of timber using wood-to-wood joinery. Prior to the discovery of metal, this is how timber posts and beams were connected to frame the homes, barns, and businesses our ancestors lived and worked in. Held together without nails, bolts, or metal connectors—timber frames tend to withstand the test of time—many with a lifespan measured in centuries instead of decades.
What is a timber frame? Learn more.
What’s the difference between timber frame and post and beam construction? Learn more.
Glue-laminated Timber (glulam)

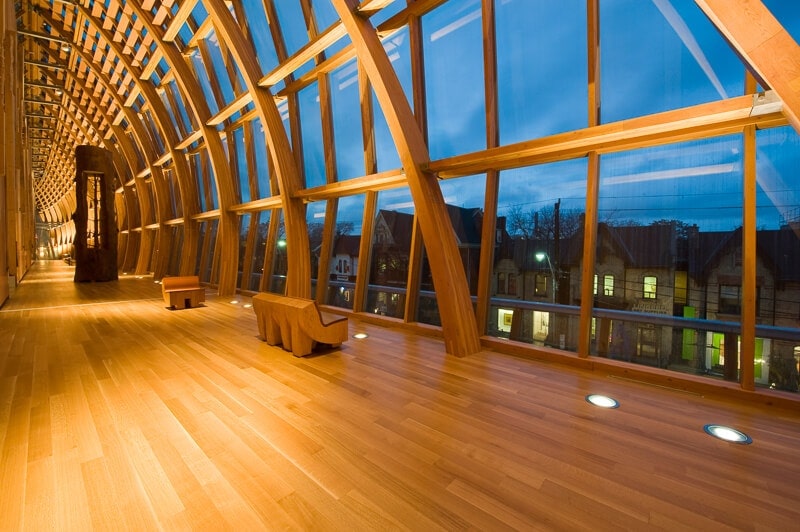
Glued laminated timber (glulam) is an engineered wood product made by laminating smaller pieces of solid lumber together with moisture-resistant adhesives into a single, usually large and very strong, structural member. These large structural members are used to create vertical columns, horizontal beams and floors, as well as curved arches.
Glulam technology allows architects to design bold curved shapes, in a range of wood species and appearances. And because of their strength and stiffness, glulam timbers can be used to create beams and arches that span large distances—up to 300 feet—without using supporting columns.
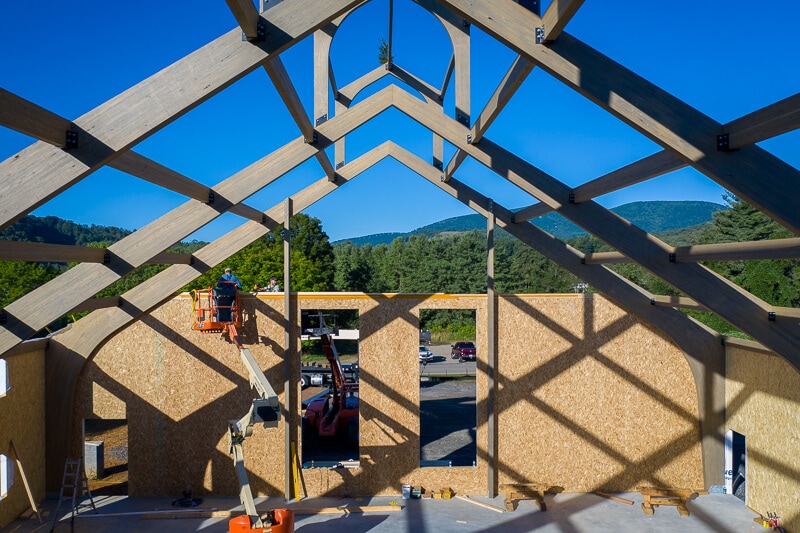
Cross-laminated Timber (CLT)
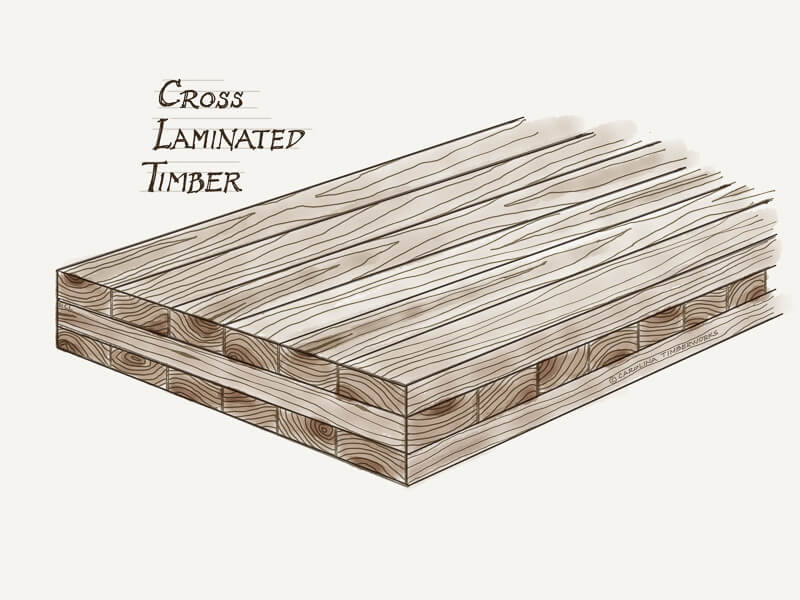
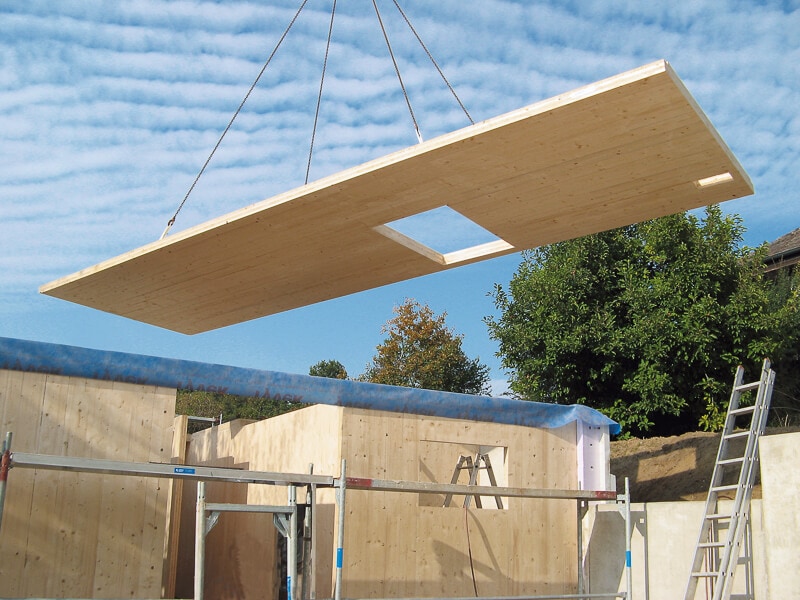
CLT was first developed in Germany and Austria in the early 1990s in response to an increasing shortage of old-growth timber. A CLT is a large, prefabricated, engineered solid-wood panel commonly used for long spans in walls, floors, and roofs. Finished panels are typically 2 to 10 feet wide, with lengths up to 70 feet and thicknesses up to 20 inches. They are light-weight and very strong, with superior acoustic, fire, seismic, and thermal performance.
CLT’s are manufactured by combining layers of lumber boards which are stacked in alternating directions, then bonded with structural adhesives, and finally pressed together to form a solid rectangular panel. CLT’s are fast and easy to install, and because they are engineered and fabricated offsite, do not generate any waste at the jobsite. As an alternative to traditional concrete and steel, CLT’s are eco-friendly, offer increased design flexibility, provide better thermal insulation, and lower construction costs due to prefabrication. Did we mention that they are beautiful to look at?
Nail-laminated Timber (NLT)
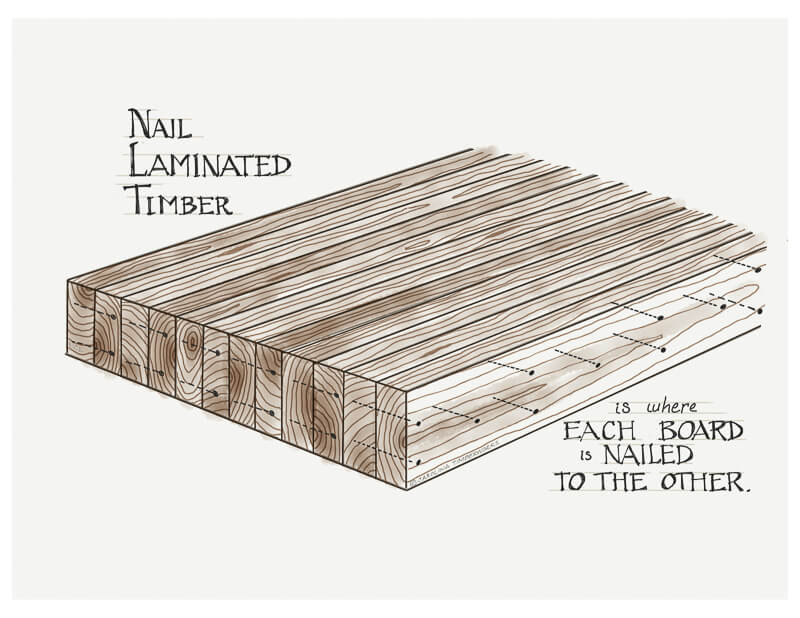
Nail-laminated timber (NLT). NLT has been around for more than a century, and used to be known as heavy timber or mill decking. To create an NLT, you simply stack layers of dimensional lumber on end and fasten them together with nails or screws. NLT is commonly used in floors and roofs as a valid substitute for concrete slabs and steel decking, with the added benefit of creating a unique, exposed wood aesthetic.
Whereas CLT is a newer technology in North America, and not always fully understood by building inspectors, NLT works well for simple spans—it’s also less expensive, and is firmly accepted in the building codes. The downside? Your saw is not going to be happy if you have to cut openings in NLT panels.
Dowel-laminated Timber (DLT) (no glue, no nails)
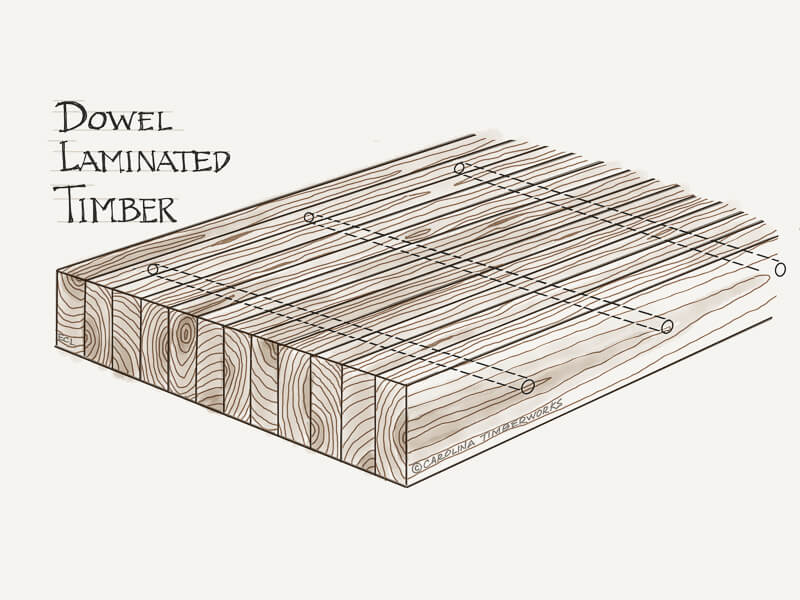
Dowel-laminated timber (DLT). The same as NLT, except instead of using glue or nails to fasten the lumber, wooden dowels are used. A major benefit is the lack of off-gassing from adhesives.
Why invest in mass timber?
Besides offering a low-carbon alternative to traditional building technology, the exposed wood interiors in mass timber buildings are warmer than other materials and far more aesthetically pleasing that concrete and steel. People love them, and literally want to hug the wooden interiors. This is because there’s still no other building material quite as warm and welcoming as wood.
In addition to the calming psychological effects of living in a wooden building, there are the physiological benefits. The buildings actually smell of wood, usually pine and spruce.
One last reason might convince you to consider CLT—the business case—developers and builders using mass timber are getting a lot of attention.
If you are getting really inspired about wood buildings, we recommend watching Michael Green’s TedTalk on “Why we should build wooden skyscrapers”
Carolina Timberworks is proud to design, fabricate, and install timber framing, glulams, and CLT panels anywhere in the United States, starting in our home of North Carolina. Send us a message or call us at 828-266-9663 to learn more.
Inquiries
Architect Contact
Curious about how buildings can be part of the solution to climate change? Read our review of Bruce King’s book, The New Carbon Architecture.
Timber Frame Construction vs. Post and Beam Construction
At first glance, timber frame and post and beam structures may appear similar. After all, both rely on heavy timber to create open spaces with exposed beams. Yet the difference between timber frame and post and beam construction is the way the individual parts are connected:
- Timber framing uses wood joinery and rarely uses steel parts
- Post and beam structures use metal fasteners and connectors
What Is Post and Beam Construction?
Post and Beam Essentials
To understand post and beam structures, it’s important to understand the difference between beam vs. post. Post and beam structures are built with vertical beam posts and horizontal beams. Metal brackets and steel plates join the timbers and hold the structure together, but they aren’t always visible. In some cases, they’re decorative, but in other cases, they’re structural and placed out of sight.
Pros of Post and Beam
Post and beam building generally has lower-skilled labor costs than timber frame construction. Although post and beam structures require plenty of labor, they tend to be less complex in engineering, construction, and fabrication. Additionally, decorative or structural metal plates can add a specific style to a post and beam structure.
Cons of Post and Beam Construction
Moisture can condense on steel surfaces, causing the steel to rust and the surrounding wood to decay. Depending on the complexity of the metal plates, steel post and beam construction material costs can be more expensive than traditional timber framing. Dissimilar materials (metal and wood) also tend to work loose over time.
What is Timber Frame Construction?
Timber Frame Construction Essentials
Timber frame construction relies on wood-to-wood joinery—so there’s no need for metal brackets. The timber frame is almost always exposed, creating a space that’s simultaneously open and cozy.
Pros of Timber Frame Construction
Usually (but not always), timber frames are more attractive, elegant, and expensive than post beam structures. Traditional wood-to-wood joinery, if kept dry, can endure for centuries. In addition, traditional wood joinery is somewhat elastic–in other words, it can deflect and give a little under loads. This is one reason that certain examples of Japanese architecture have survived for over a thousand years–despite the destructive earthquakes that occur several times each century.
Cons of Timber Frame Construction
Timber framing has a higher cost of skilled labor to design, engineer, and fabricate traditional joinery. Some structures increase timber cost when timber sizes increase, which may occur during engineering to accommodate joinery.
Post and Beam vs. Timber Frame
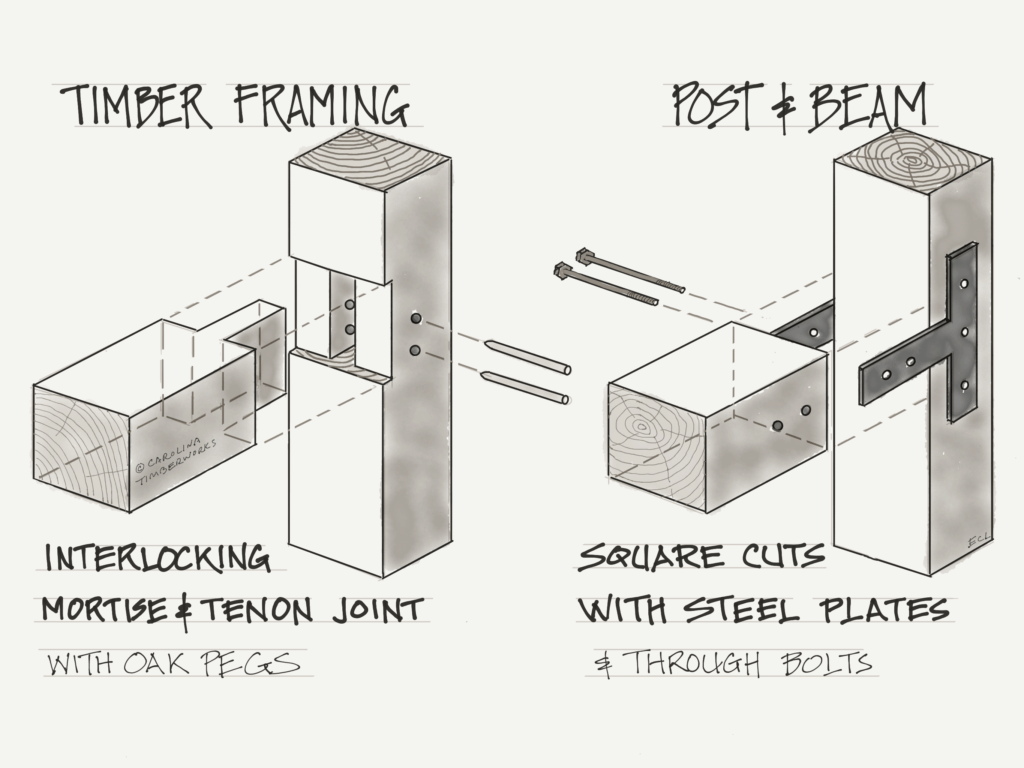
What Do Both Methods Have in Common?
Ultimately, timber frame and post and beam structures have a similar visual style. Both tend to create open spaces with exposed beams and natural elegance. That’s because both types of construction use heavy timbers rather than 2x4s.
How Joinery Makes a Difference in Construction
Some timber framers believe that wood should be the only component in a true timber frame structure. When it comes to timber frame construction, mortise and tenon joinery bring everything together—both aesthetically and structurally.
In contrast, post and beam construction uses metal plates and bolts. While that may not seem like a big difference, some would argue that this method isn’t truly timber framing.
Learn More: Our Timber Frame Glossary
Timber Frame Trusses Guide
truss, n. A collection of timbers or members forming one of the principal supports, as of a roof or bridge, and framed together so as to give mutual support and prevent distortion, as by the forces of gravity and wind loads.
Wood trusses, whether structural or decorative, are usually named in one of five ways: 1. from the construction in which they are used; as in, roof truss or bridge truss, etc.; 2. from their form; as in, lenticular truss, etc.; 3. from their resemblance to certain objects; as in, scissors truss, etc.; 4. from some prominent feature in their construction; as in, king post truss, hammer beam trusses, etc.; 5. from the person by whom they were in invented; as in, Howe truss, etc. (adapted from the Funk & Wagnalls Company 1943 Standard Dictionary of the English Language)
Timber Frame Truss Types
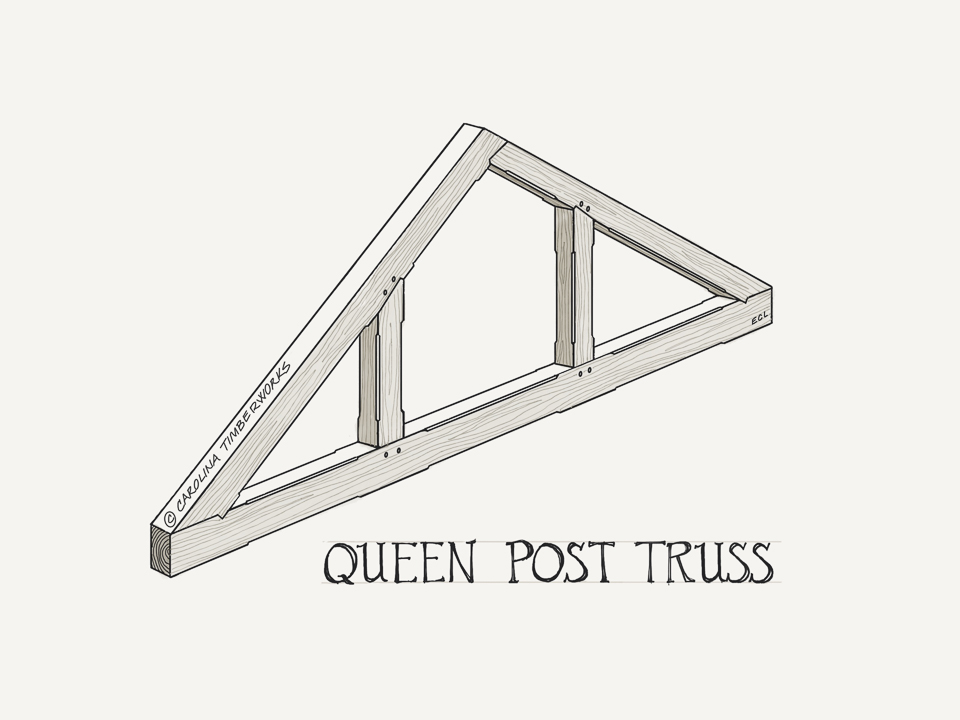
Queen Post Truss
The queen post truss with with paired queen posts is a classic truss design, with many variations. The basic double posted version may also have a horizontal crossmember between the two verticals. Additionally, diagonal braces and/or struts may be added for increased strength and visual appeal.
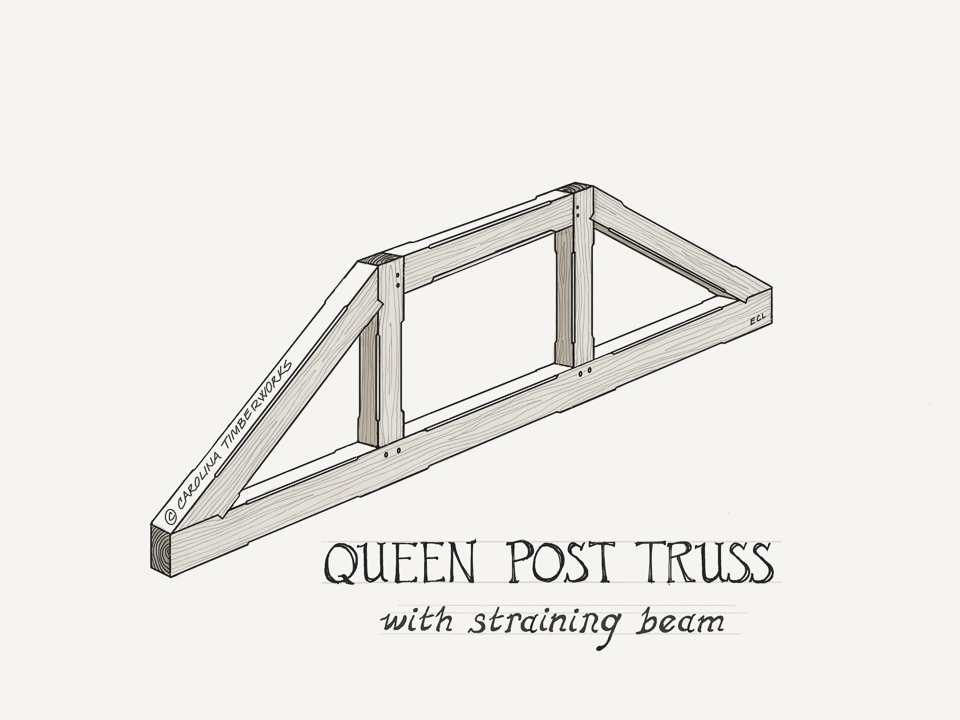
Queen Post Truss with Straining Beam
The queen post truss with straining beam between the tops of the posts (the true queen post truss), forms a configuration capable of much longer spans. Wood trusses of this type have been developed for distances over 50′. Straightforward geometry and pleasing lines make it timeless and honest.
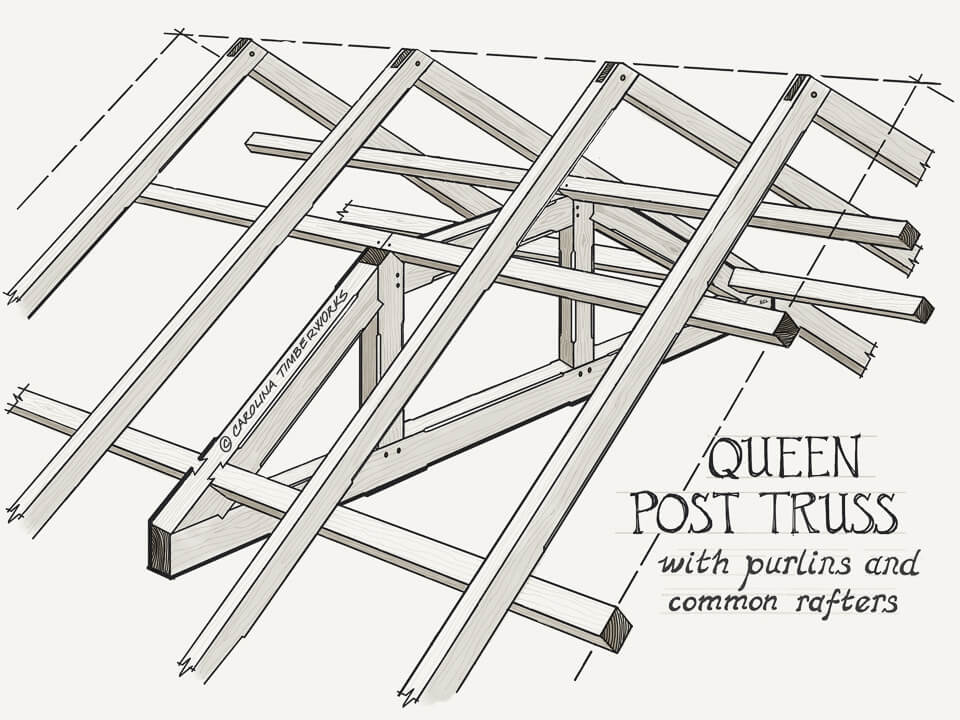
Queen Post Truss with Purlins and Common Rafters
Queen post trusses can be integrated with smaller members to form a more complex roof system. In this version, purlins are placed between wood trusses, to support pairs of common rafters above. These 3 components merge aesthetics and structure to create a striking multi-layered timber frame roof. Note that the tops of the purlins are a great place to hide indirect lighting.
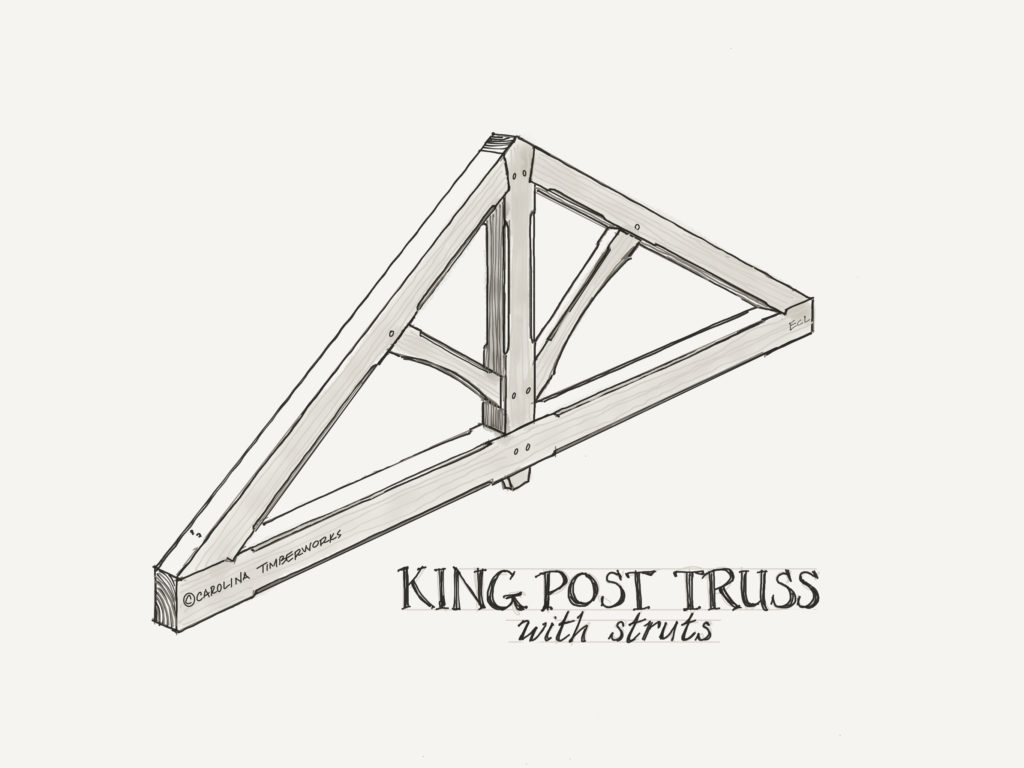
King Post Truss
The king post truss with struts is popular, timeless, very strong, and an elegantly simple truss design. This style can be embellished with radius cuts on the struts and a through tenon at the base of the king post (as pictured above). This truss is very adaptable with regard to desired span and roof pitch.
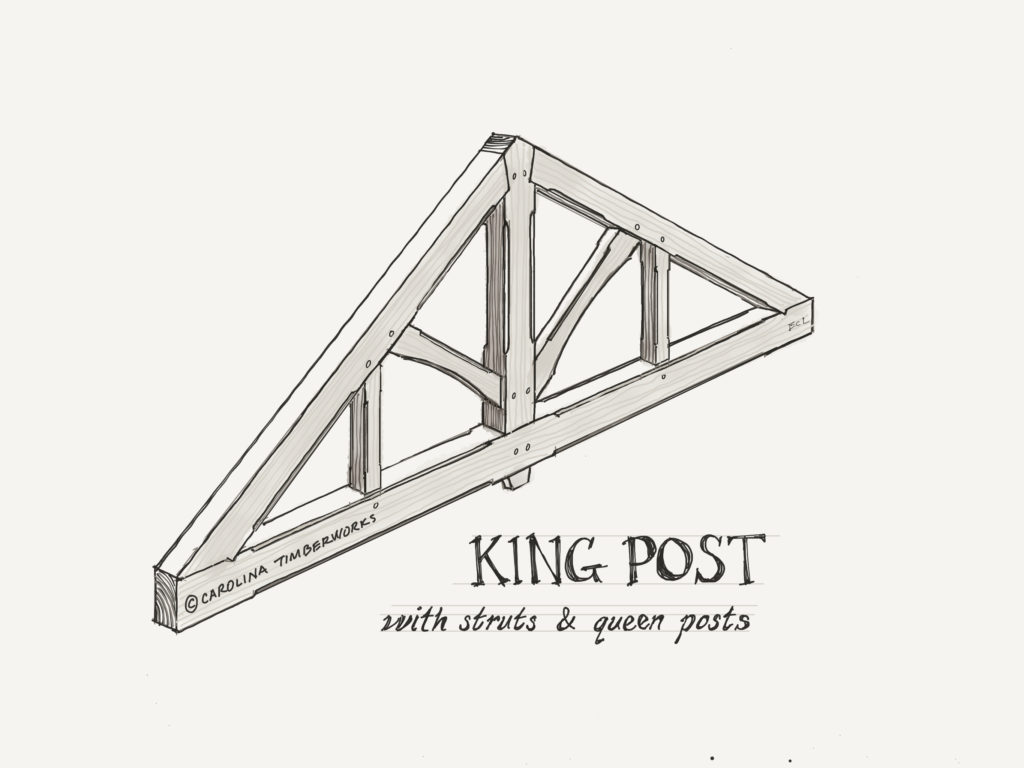
King Post Truss With Struts and Queen Posts
The king post truss with struts & queen posts is based on the popular king post truss design, but with the addition of two queen posts (pictured above). This timber truss is also very strong, and adaptable with regard to desired span and roof pitch. This arrangement is particularly good for longer timber frame truss spans (in excess of 24’ feet).
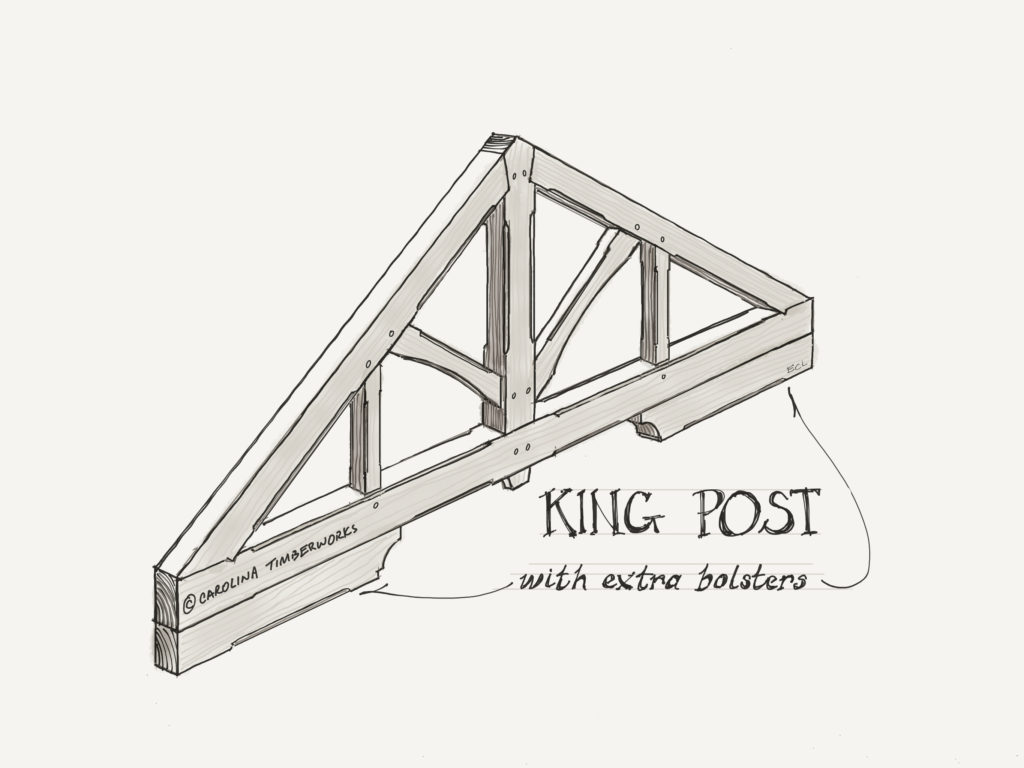
King Post Truss With Extra Bolsters
The king post truss with extra bolsters builds on a favorite timber truss design with two added bolsters on the underside of the bottom horizontal chord for a heftier look. These mirror image pieces added to the underside of the bottom chord can provide a stepped transition to the vertical wall plane. The bolsters can have a wide variety of decorative profiles cut into their visible ends. Twin metal straps can also be banded around both the bolster and the bottom chord for a craftsman detail.
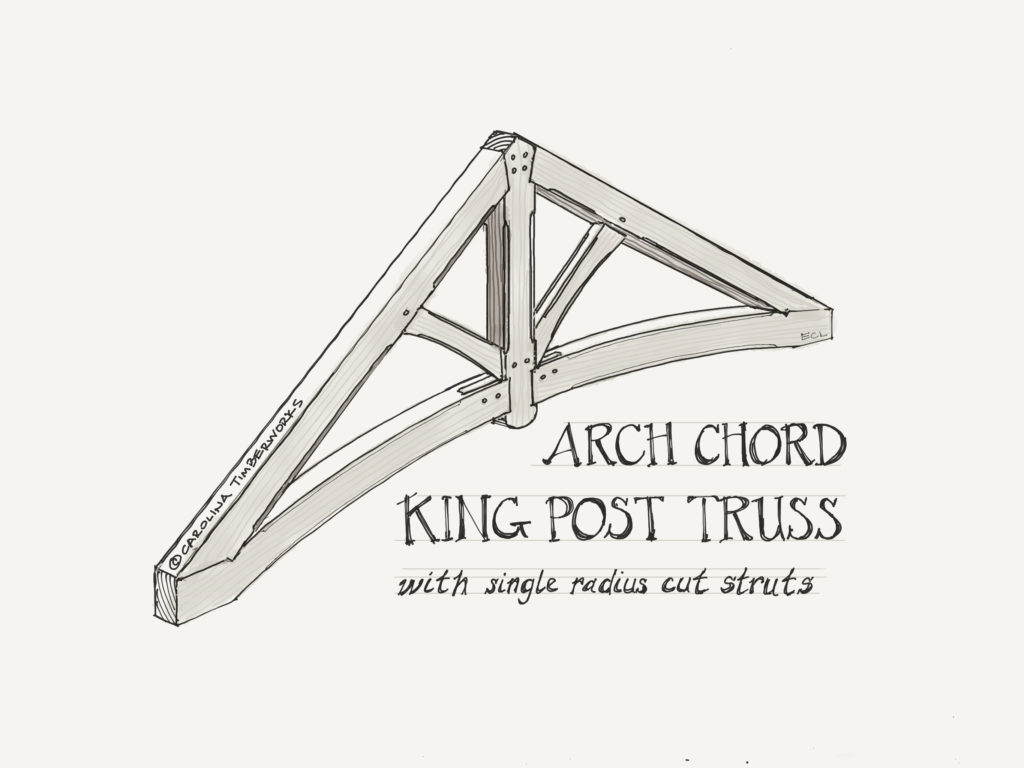
Arch Chord King Post Truss
An arch chord king post truss is another variation on the classic king post style, this time with an arched lower chord. This design adds a curvilinear element into the ceiling space instead of the standard horizontal timber, raising the structure somewhat and giving some extra volume below. Some of our clients have pointed out how the curves in this timber frame truss soften the lines and convey a natural aesthetic (after all, there are very few straight lines in nature). The radius cut for the arch should be shallow in order to be cut out of solid sawn timber. However, more semi-circular arches can be accommodated by using a grain matched glue laminated arch material (this is considerably more expensive than solid sawn timber).
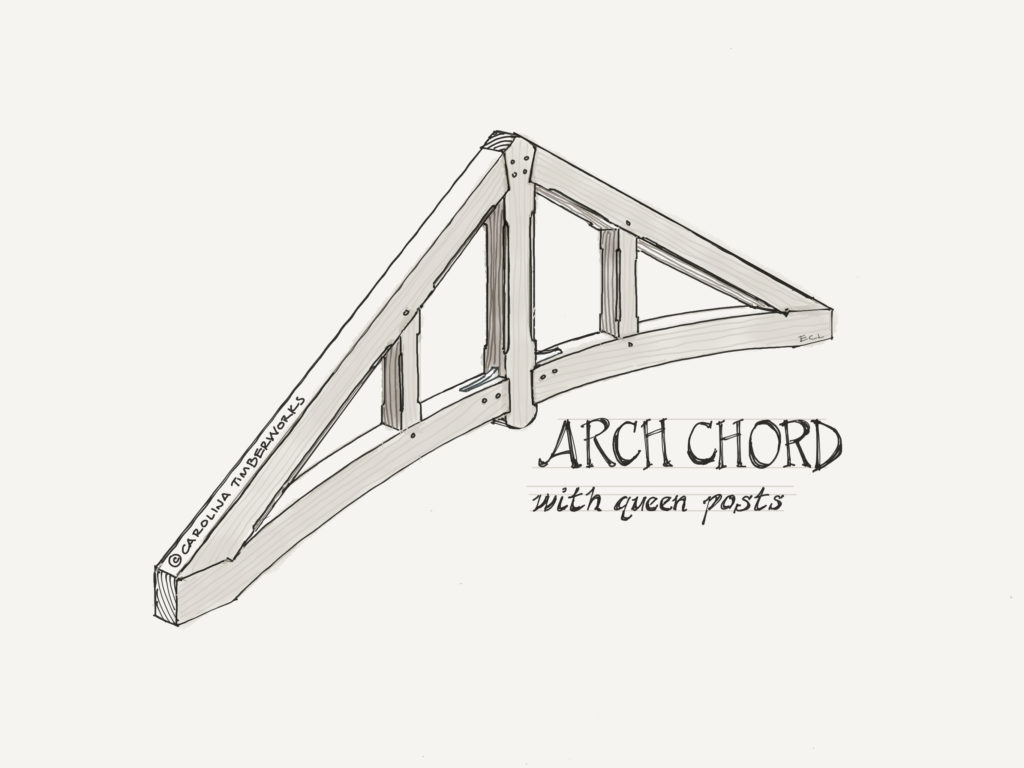
Arch Chord With Queen Posts Timber Frame Truss
The arch chord with queen posts timber frame truss is another variation on the classic king post style, this time with twin vertical queen posts. This design adds more vertical elements above the arched bottom chord with the extra volume below. The radius cut for the arch should be shallow in order to be cut out of solid sawn timber. We like to use a spline tenon to joint the 2 half arches to the base of the king post. On larger spans, this configuration often requires concealed steel connectors to resist tension and spreading along the arch itself.
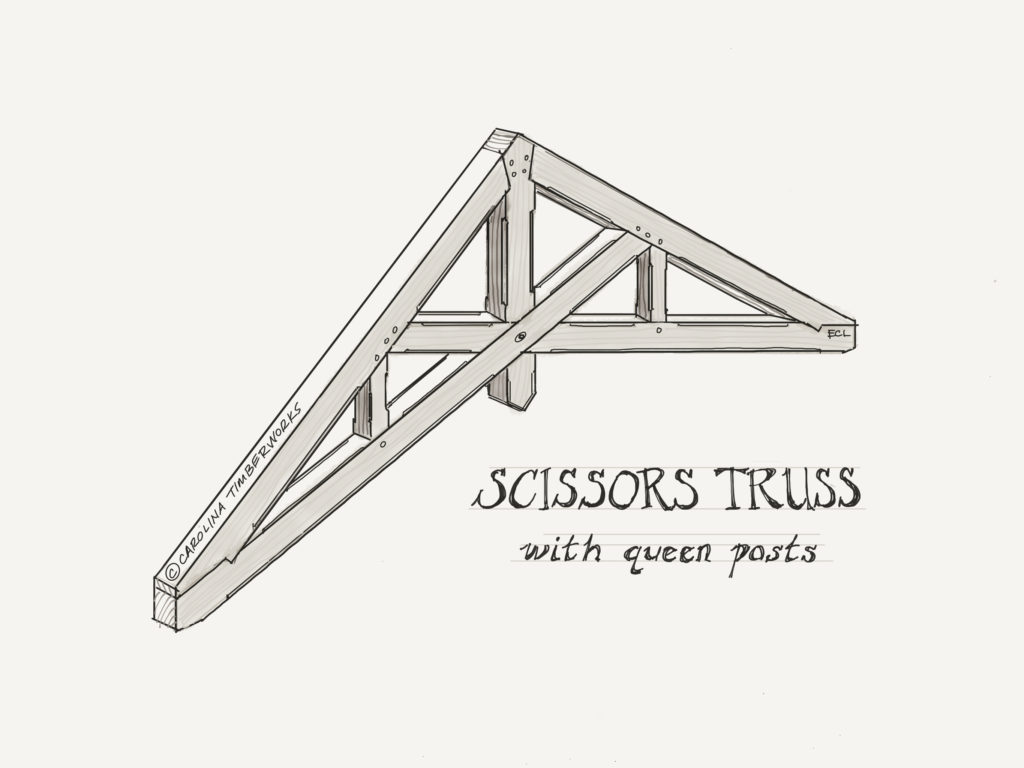
Scissors Truss
A scissors truss is a traditional truss style with many variations, this design can be used in small or large spans. Scissors trusses are not recommended for shallow roof pitches ( below 8/12 pitch ). We like to add the queen posts on either side of the central king posts. These timber frame trusses have a more complicated geometry with many angled intersections and a higher center for added space.
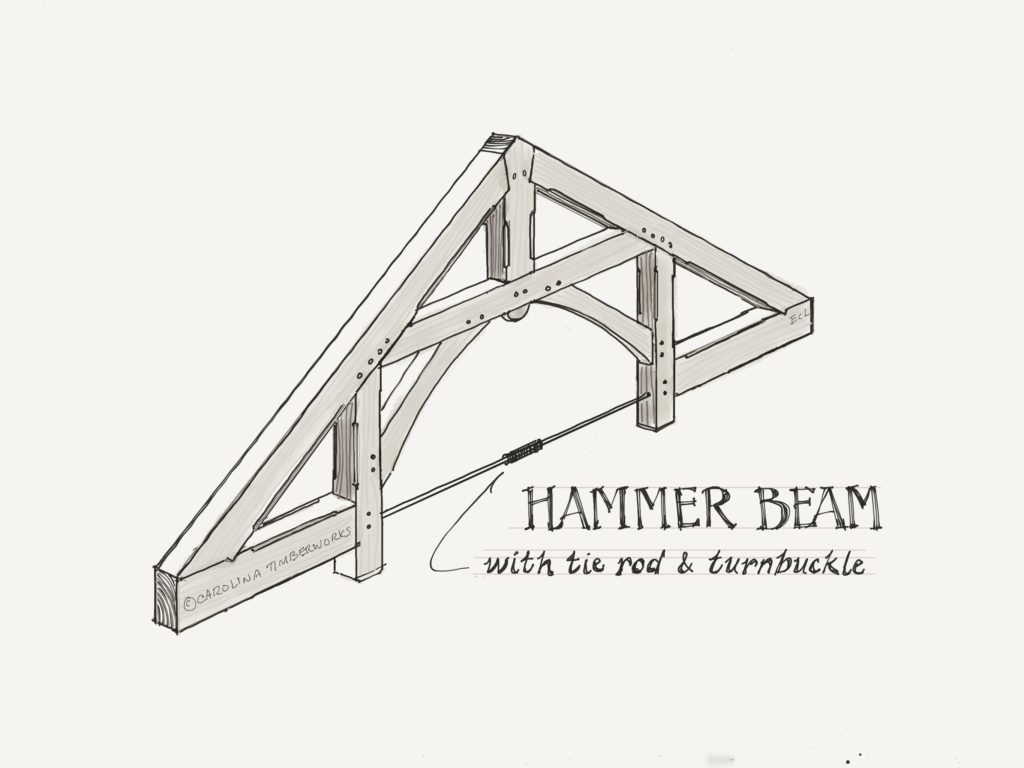
Hammer Beam Truss
A hammer beam truss is based on the more elaborate hammer beam timber frame bent design. The combination of heavy timber and metal tie rods and turnbuckle is not only appealing but is often required to handle the spreading forces this configuration will develop. In case you were wondering, a hammer beam is a short beam projecting laterally from the inside of a wall, and serving as a tie beam.
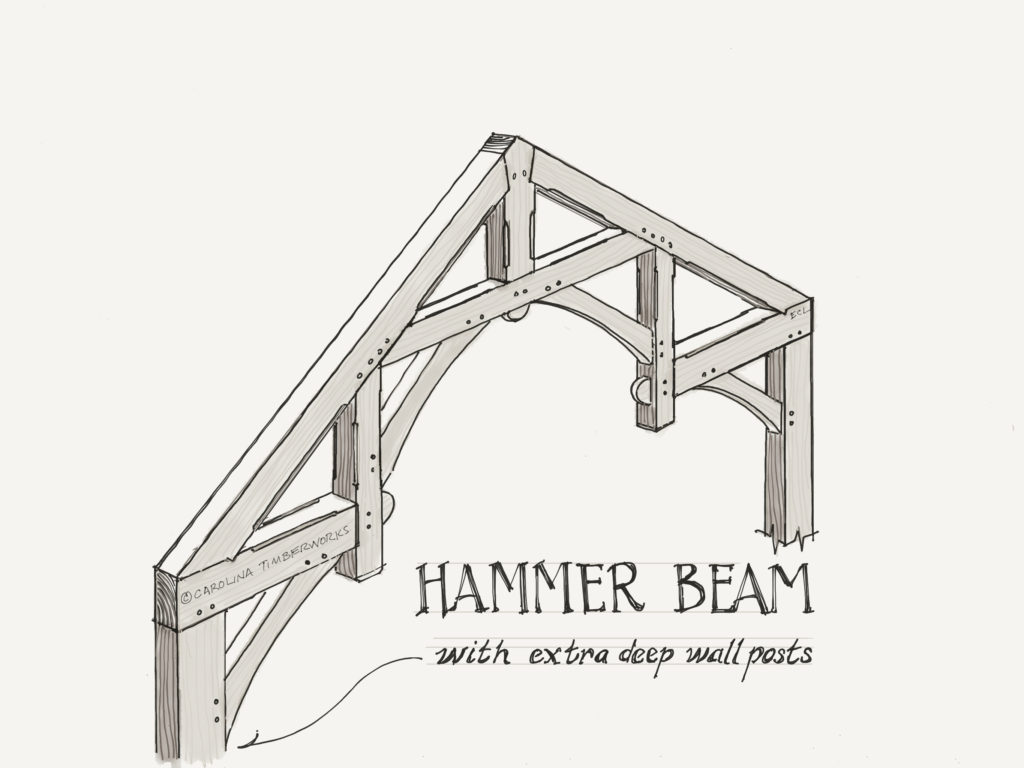
Hammer Beam Truss
A hammer beam truss, pictured above, is a beautiful and more complicated design, and creates dramatic vaulted spaces. There are many ways to embellish this design, from through tenons and radius cuts to decorative pendants or finials. The hammer beam bent is often associated with religious structures, great halls, or great rooms. Without a metal tie rod and turnbuckle, deep wall posts and/or concealed steel connectors are needed to handle the forces this configuration will develop.
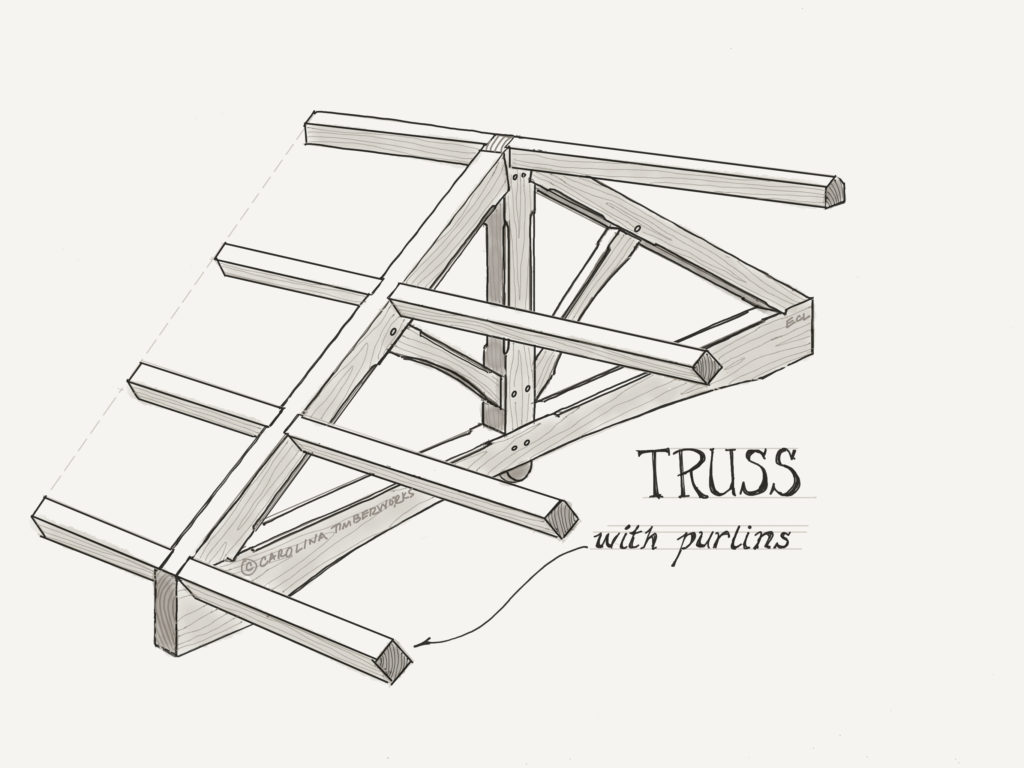
Truss with Purlins
Truss and purlins: adding purlins between heavy timber trusses is an elegant way to reduce the cost of a timber frame roof because purlins permit an increased on-center distance between trusses (so you purchase fewer trusses). An added benefit are the strong lines that purlins create by running parallel to the ridge beam(s). (Another benefit is that purlins are a great place for placing LED lighting fixtures). Purlins often sit in pockets cut into the truss rafters (as shown) but can also sit on top of the truss rafter to create a secondary layer to the roof structure. There are some span restrictions based on the purlin size ( beam width x depth) and how close they are together. This is a very traditional concept in heavy timber roof framing. (purlins are a series of horizontal timbers laid across (or connected to, as depicted above), the principal rafters, and support the roof covering–typically 2×6 tongue and groove boards, conventional or structural insulated panels (SIPs), and roofing)
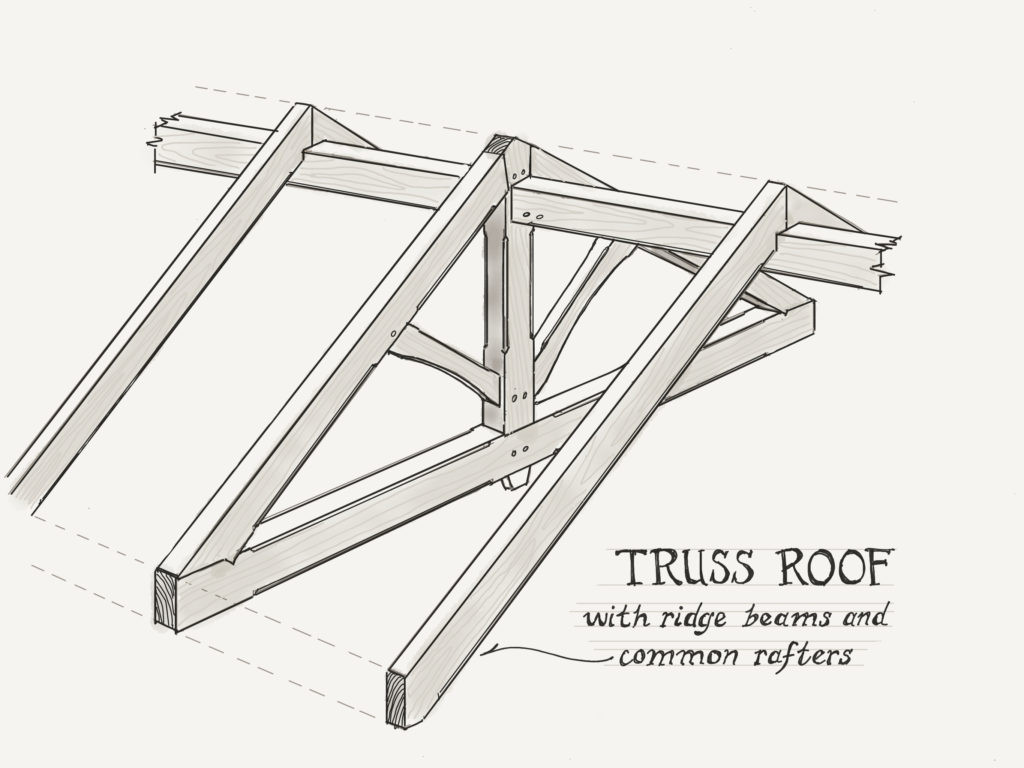
Truss Roof With Ridge Beams and Common Rafters
A truss roof with ridge beams and common rafters can provide a larger space between each truss. We like common rafters between each truss thereby giving a rhythm to the roof structure. The common rafters are often smaller than the truss timbers to differentiate between the primary and secondary timber frame elements.
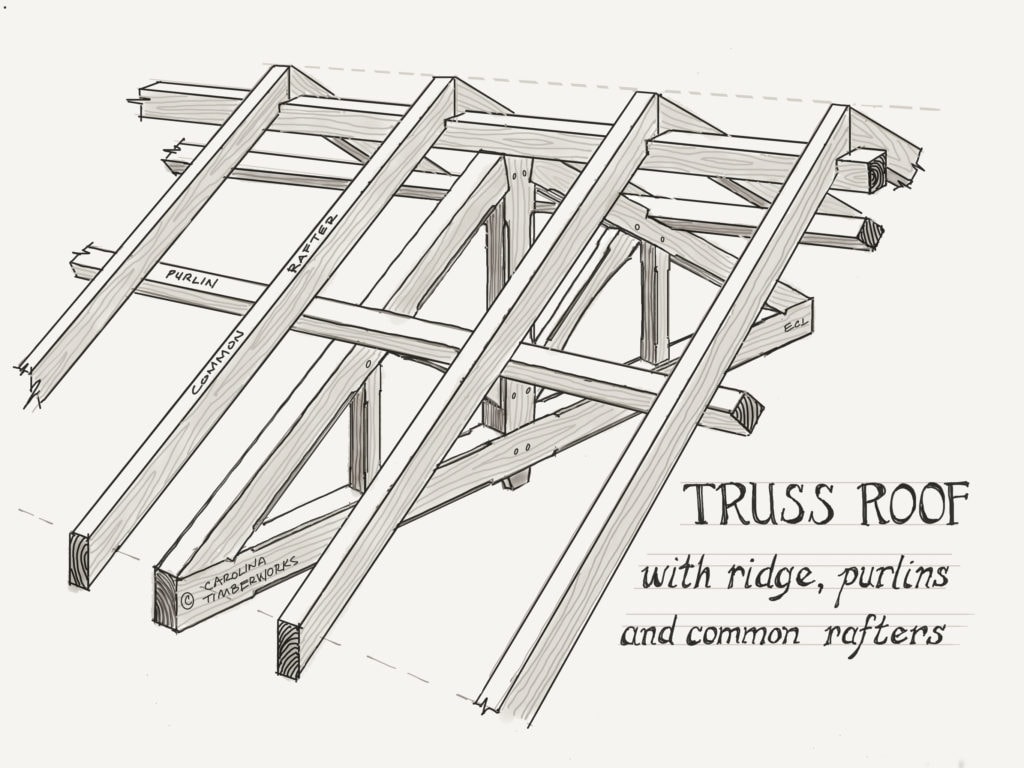
Truss Roof With Ridge Beam, Purlins, and Common Rafters
A truss roof with ridge beam, purlins, and common rafters is a stunning combination that creates visual interest and structural complexity. There is a hierarchy of timber framing at work here, with trusses supporting the ridge and purlin beams. Above these components is a rack of common rafters. Typically wooden trusses are made from the biggest timbers, followed by intermediate sized ridge and purlins followed by the common rafters as the smallest timbers. One of our favorite combinations!
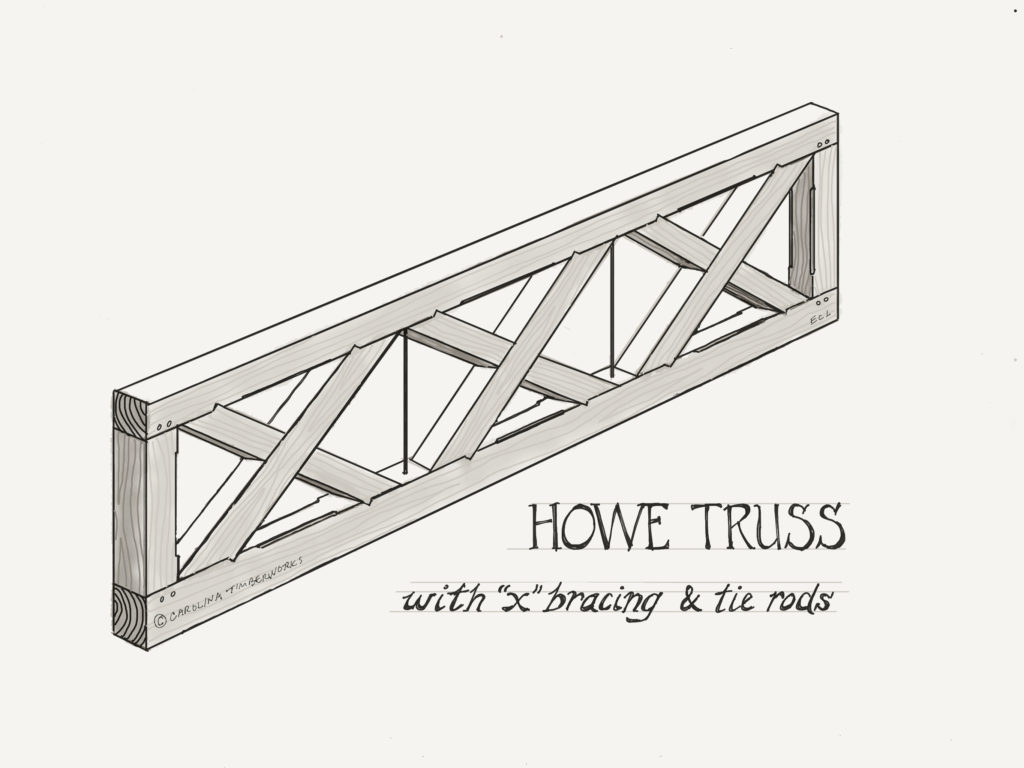

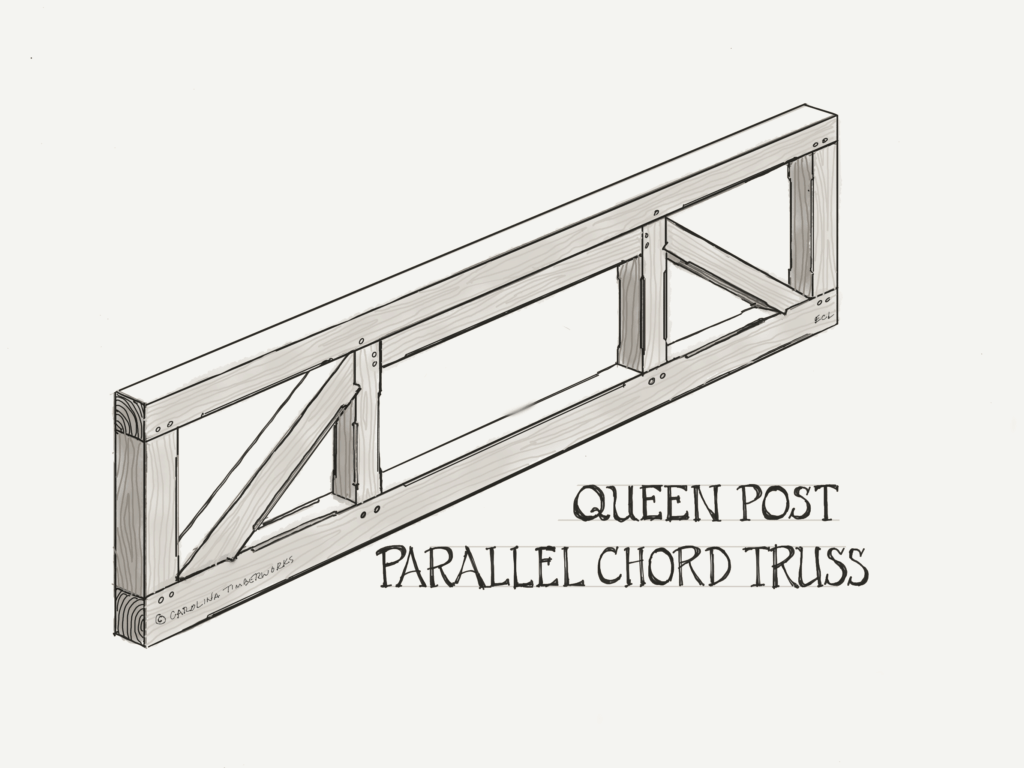
Bridge Trusses
The Howe, Warren, and Queen Post Parallel Chord Trusses, sometimes referred to as Bridge Trusses are relatively simple designs used in the construction of everything from the earliest 19th century modern bridges to WW II aircraft hangars. They’re efficient, strong, and characterized by the joining of numerous smaller members into a series of interconnected triangles. In addition to being a proven way to solve the engineering problem of long spans, we think they look great in modern timber framing (see an example here) and are one of the best examples of form following function.
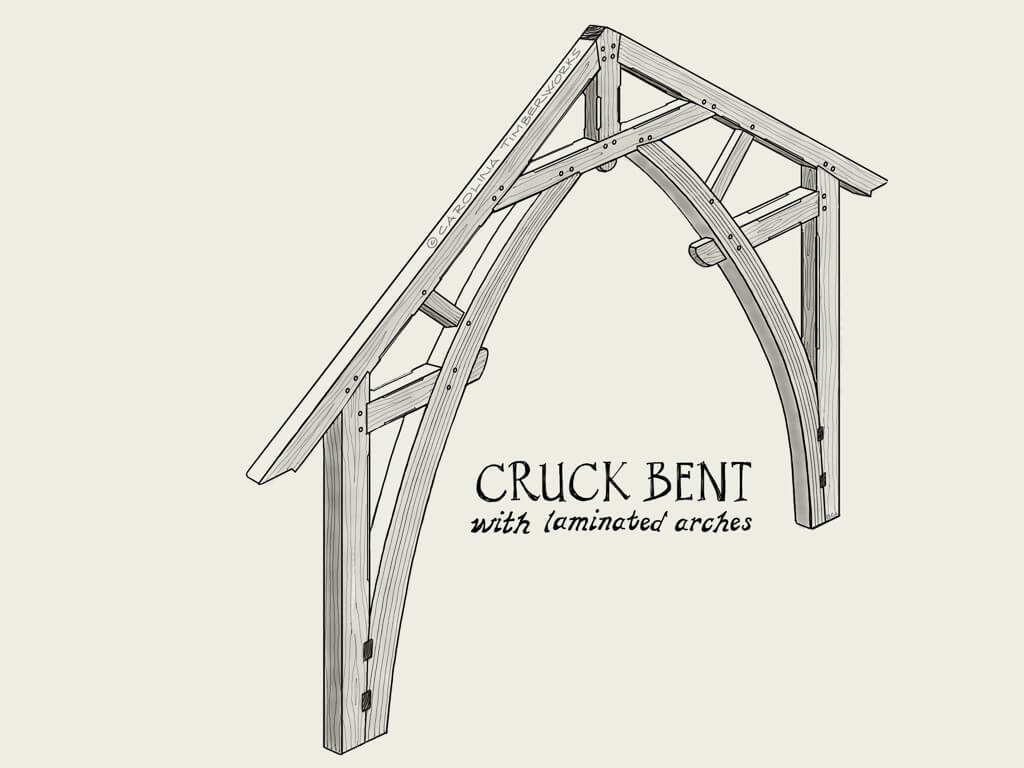
Cruck Frame Bent
Cruck Frames, found primarily in the UK, were the original A-frame. According to Cruck Building: A Survey, the definitive definition of a cruck is as follows: “a true cruck consists of a pair of timbers (blades), straight or curved, serving as the principals of a roof, and stretching to point at or close to the apex of the roof, from a level well down the side walls.”
Learn More: Our Timber Frame Glossary
Copyright 2019 Carolina Timberworks. All rights reserved. Illustrations by Eric Lubsen.
Timber Frame Trusses Inquiry
What is the Best Wood for Timber Framing Projects?
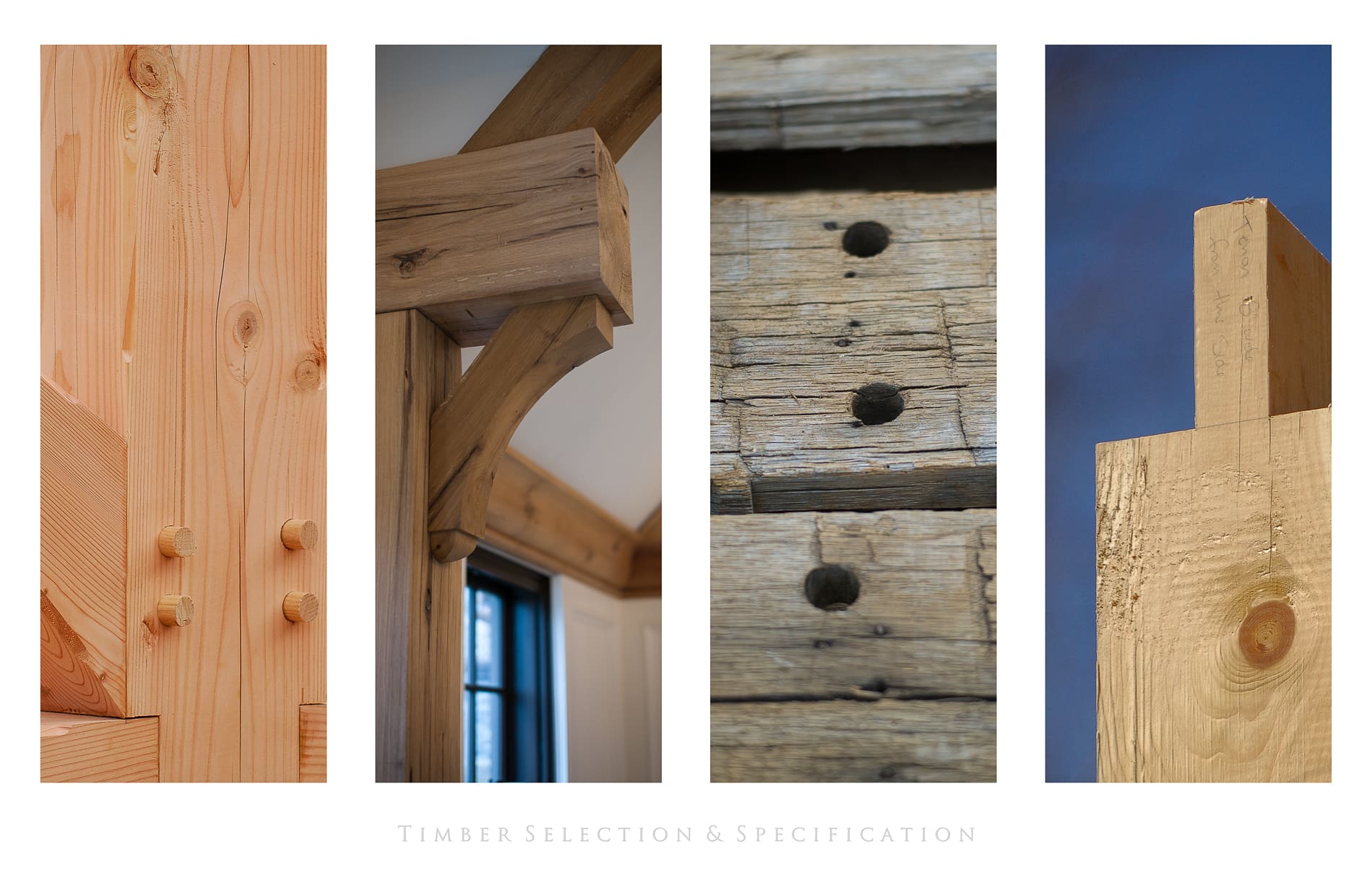
We’re often asked, “What is the best wood for timber framing?” Although it’s estimated that 60% of timber frames in North America are built from Douglas fir, there are other timber frame wood species that may work as well, or better, for your building project.
So, here in one place, is exactly how to select a timber species from the most common woods used in timber framing. Perhaps as important, you’ll learn how to specify the other important wood characteristics for a timber frame — things like timber grade, moisture content, heart content, and surface texture.
What Type of Wood is Used for Timber Framing?
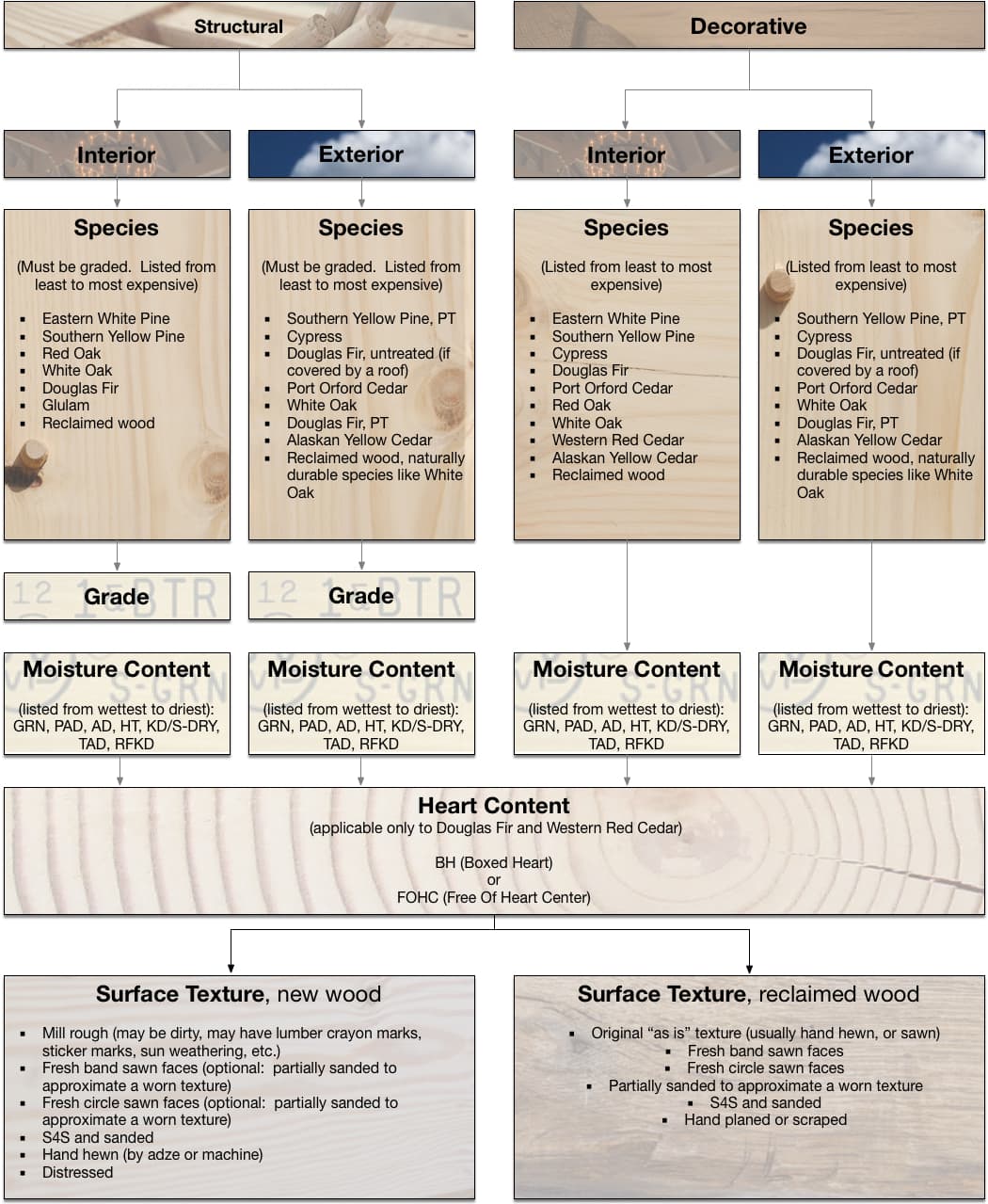
Common Timber Frame Abbreviations
- AD: air-dried
- BH: boxed heart
- FOHC: Free of Heart Center
- Glulam: glued laminated timber
- GRN: green (freshly cut, wet)
- HT: heat-treated (reclaimed wood is sometimes heat-treated to kill bugs)
- KD: kiln-dried (when timber is dried in a conventional kiln, only the outer inch or so is dried)
- PAD: partly air-dried
- PT: pressure-treated (with chemicals to resist decay)
- RFKD: radio frequency kiln dried (dry to the core, but only applicable to Douglas fir
- S4S: surfaced four sides
- S-Dry: surface dry
- TAD: thoroughly air-dried
Confused by timber framing jargon? Our Timber Frame Glossary is a handy resource to make sense of it all.
Characteristics of Common Timber Frame Wood Species
For each of the common timber frame materials used in the construction below, we’ve noted the characteristics, decay resistance, and the relative cost ($ less costly, $$ average, $$$ more costly). Some of the information below is adapted from the USDA Forest Service’s Forest Products Laboratory book: Wood Handbook–Wood as an Engineering Material.
Best Wood for Post and Beam Construction and Timber Framing
The ideal types of wood for timber framing include bald cypress, Port Orford cedar, western red cedar, and eastern white pine. Bald cypress is a popular choice for wetter climates due to its moderate resistance to decay. Port Orford cedar offers a straight grain, a distinctive scent, and high decay resistance, making it a favorite for specialized architecture. Western red cedar is lauded for its very low shrinkage and natural fungicidal properties, increasing durability. Eastern white pine develops a beautiful patina over time, balancing quality with affordability.
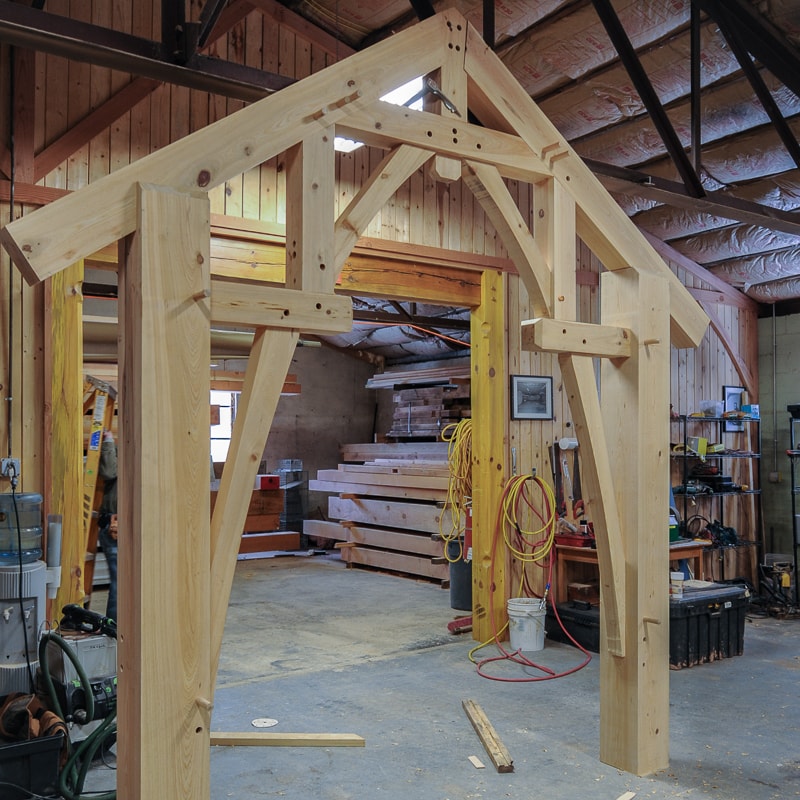
Bald Cypress (Taxodium distichum)
Also known as southern cypress, tidewater red cypress, yellow cypress (inland), and white cypress. Southern US softwood; moderately heavy, moderately strong, and moderately hard. Old-growth is resistant or very resistant to decay, but no longer readily available. Second growth is moderately resistant to decay. Sapwood is narrow and white-colored. Heartwood color varies from light yellowish to reddish-brown color. Shrinkage is moderately low but somewhat higher than the cedars. Difficult to obtain longer than 20′. $$
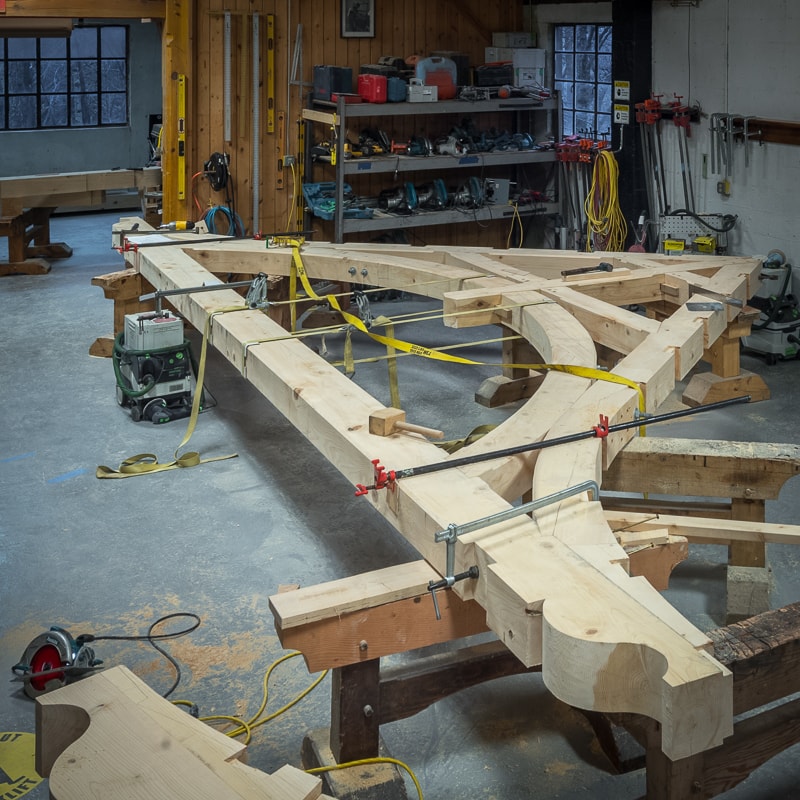
Port Orford Cedar (Chamaecyparis lawsoniana)
Straight-grained, fragrant, and durable. A softwood that grows along the Pacific Coast from Coos Bay, Oregon, southward to California in a narrow band less than 40 miles wide. Fine texture, generally straight-grained, with a pleasant spicy odor (it reminds us of ginger). Moderately lightweight, stiff, moderately strong, and hard. The heartwood is highly resistant to decay. Moderate shrinkage with little tendency to warp. Prized by Japanese temple builders as it resembles Japan’s sacred and rare, Hinoki Cedar. $$

Western Red Cedar (Thujaplicata)
Straight grained, low shrinkage, durable. A softwood that grows in the Pacific Northwest and along the Pacific Coast to Alaska. The heartwood is reddish or pinkish brown to dull brown, and the sapwood is nearly white. Narrow, and usually less than 1″ wide. Very low shrinkage, lightweight, moderately soft, low in strength. The heartwood is very resistant to decay because the chemical substance Thujaplicin, found in mature western red cedar trees, is a natural fungicide. $$$
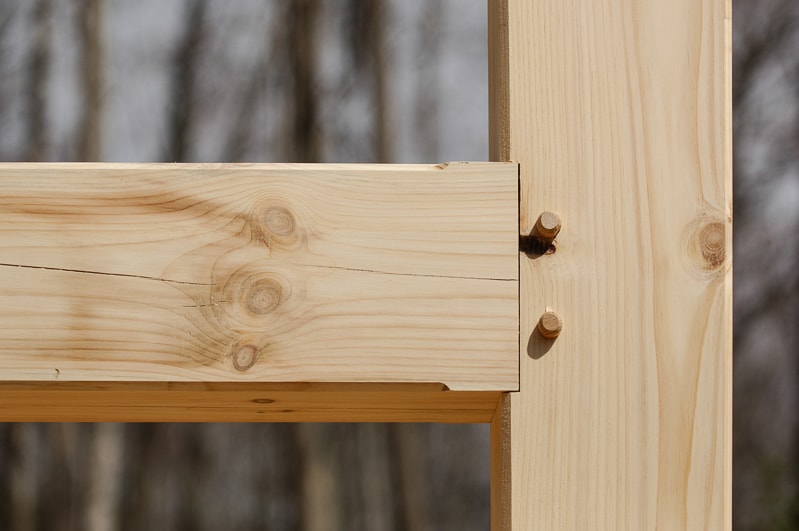
Eastern White Pine (Pinus strobus)
The “moderate” timber: moderately soft, moderately low in strength, moderately durable, and moderate shrinkage. A softwood that grows from Maine to northern Georgia and in the Great Lake States. Challenging to obtain graded for structural timber framing. Creamy white or pale straw to light reddish-brown. Darkens with time to a light caramel color, then after many years to a deep rich golden tan. Stains well. $
Learn More: Our Timber Frame Glossary
Why Do Timbers Split and Crack?
Eric Morley on why timbers split and crack, how long it takes timber to dry, where to get dry timbers, and why gunshots in the night are nothing to be afraid of when you understand wood checking and splitting.
Wood checking and splitting, a natural phenomenon in timber, occurs as the wood dries and loses moisture. This process leads to split wood and cracked wood, known as “checks.” While they do alter the appearance of the timber, checks also add unique character without affecting the wood’s structural integrity.
What Causes Wood to Crack?
Drying Does!
Splits and cracks (known as wood checks in the industry) occur when wood shrinks as it dries. Wood shrinks roughly twice as much along with the growth rings (radially) as it does across the rings (tangentially). It is this uneven shrinkage that causes checks to develop.
Is Wood Checking Bad?
Here at Carolina Timberworks, we think of them as wrinkles in a cotton shirt. It proves the timber is real. Checks are what make a solid timber look different from a boxed beam. Look at the reclaimed timber below. It is impossible to predict where a check will appear in timber. It is the check that gives this reclaimed white oak timber so much of its character and a big part of what makes it completely unique and different from any other beam in the world.
Ever Heard the Song of the Wood?
Have you ever taken a hot loaf of artisan bread out of the oven, and put your ear to it? If you do, you’ll hear the song of the bread–pops and crackles as the crust shrinks, cracks, and dries.
Walk into a timber framer’s shop one winter evening when everyone has gone home for the day. Throw another log into the woodstove, and listen carefully. If there are green (wet) timbers arrayed on sawhorses, within a few minutes, you’re likely to hear the song of the wood – a symphony of pops and cracks as wood checking occurs.
If one night, asleep in your new home, you’re awoken by a loud crack a little like a gunshot. Don’t worry. Roll over and go back to sleep. It’s just your timbers singing to you. That’s wood checking in action.
Why Does Wood Shrink?
It sometimes surprises people to learn that roughly half of a living tree’s weight is water. Let’s consider a 24’ long Douglas Fir log that measures 34” diameter at the large end and 14” at the small end as an example. This hypothetical green (wet) log would contain a little over 1 ton of water or about five 55-gallon drums of water.
Sometimes when we drive a chisel into green (wet) timber, water spurts out of the wood. Wood is hygroscopic – meaning it’s like a sponge in that it can absorb, hold and release water. When freshly cut, approximately half of a tree’s weight is water. The photograph below shows water in a freshly cut cypress timber–and how the timber is drying from the outside in.
How Long Does It Take a Timber to Dry?
It’s not exactly a fast process. It depends on the humidity of the environment in which the timber is located, but a rule of thumb is that timber air dries about one inch per year. Thus a 12” x 12” timber would take about six years to dry to the center.
How Dry Will the Timber Become?
A timber will eventually air dry to the Equilibrium Moisture Content (EMC) of its environment. The EMC is the point at which wood is neither losing nor absorbing water. A timber’s moisture content is determined by the atmospheric humidity of the timber’s environment.
That environment varies, of course. Is the timber located inside, or outside? What part of the country is it located in? What time of year is it? For example, in the dry mountain air of Denver, the outdoor EMC of wood exposed to the outdoor atmosphere in July is 9.4%, while New Orleans is 15.3% (Forest Products Laboratory: Equilibrium Moisture Content of Wood in Outdoor Locations in the United States and Worldwide, August 1988).
How Wet (or Dry) Are My Timbers?
Since we can’t see the water in the wood, moisture meters are used to measure moisture content. Inexpensive moisture meters measure the surface moisture content which works ok for 3/4” boards, but not 8” thick timbers. Professional moisture meters use electromagnetic scanning to read the moisture in the wood, not on the surface of the beam.
What is the Average Moisture Content in the U.S.?
The majority of the U.S. has an 8% average moisture content, the Southeast and California coastal areas have an 11% average moisture content, and the Southwest desert areas are closer to 6%.
Most Timber Frames Are Built From Green (Wet) Wood
It is impractical (it takes years) to air dry timber, and timber frame customers are nothing if not impatient, so for the last two thousand years, people have been building timber frames from green (wet) timber. Yes, green timber will shrink, check, and sometimes twist as it dries, but timber framers and engineers understand and account for the movement. Checks begin on the exterior surface of the timber and almost always stop at the heart (center) of the timber, and are almost never a structural concern.
By the way, if a crack were to develop all the way through a timber (splitting timber it into two separate pieces), it would be called a split and might be cause for concern.
Learn more about timber framing all the ways timber can be used here.
How Much Does Green (Wet) Timber Shrink as It Dries?
Shrinkage depends on the species, but more than you may think!
Since many timber frames are built from Douglas Fir, let’s start by looking at a 12×12 Douglas Fir (Coastal) timber. This particular green (wet) Douglas Fir timber, dried to a final moisture content of 8%, would be expected to shrink a little less than 9/16” on each face from 12” x 12” to a final size of 11-7/16” x 11-7/16”.
Western Red Cedar shrinks less: The same size timber in Western Red Cedar timber would shrink a bit less about 5/16” to 11-11/16” x 11-11/16”. Finally, how about a species with a high shrinkage rate, like White Oak? It would be expected to shrink a bit less than 3/4” to slightly larger than 11-1/4” x 11-1/4”.
6 Ways to Minimize Problems with a Green (Wet) Wood in a Timber Frame:
- Specify Free-Of-Heart-Center (when available) instead of the lower Boxed Heart grade.
- Apply a wax-based end sealer to the end grain to slow the drying process. We use Anchorseal, available at https://uccoatings.com/products/anchorseal/.
- Utilize housed joinery wherever possible.
- Drawbore pegged joints.
- The slower the wood cracking when drying, and the more gradual the process, the better (i.e., the worst thing you can do is enclose the timber frame and immediately turn on the heat or air conditioning full blast.)
- Do not apply a film-forming finish (i.e., polyurethane) to green (unseasoned) wood.
- Sawing checking kerfs on an unseen timber face is a good practice and can help mitigate the visual checking.
I Don’t Want Wood Checking or Cracks in My Timbers. What Are My Options?
Don’t build with solid timber. Instead, ask us to price glulam beams for the timber frame, or to fabricate box beams from kiln-dried new or well-dried reclaimed lumber.
If you’re ok with some checks, but would prefer to avoid some of the characteristics of green lumber, consider purchasing your timber like you do your high-quality organic cotton t-shirts–pre-shrunk. There are two ways to buy dry beams: new timber that’s been dried in a kiln, or reclaimed wood that’s dried slowly and naturally for 50 or 100 years during its previous life as a timber frame barn or warehouse.
Where to Buy Kiln Dried Timbers?
We offer two types of kiln-dried timber: Conventionally kiln-dried (KD), and Radio Frequency Kiln Dried (RFKD). Conventional kiln drying dries about the outer 1” or so leaving most of the timber wet. The other method, RFKD, is similar to a giant microwave and dries timber to the core.
What you need to know about RFKD timber is that it currently works only on Douglas Fir, it is dry to the core, and it is more expensive. It is, however, not as dry as conventionally kiln-dried hardwood flooring or lumber (6-8% moisture content). For example the driest grade of RFKD timber measures 15% or less moisture content 3” in from the surface of the timber.
What About Using Reclaimed Wood in Timber Frame Construction?
Reclaimed wood beams that have naturally air-dried for 50-100 years during their previous life as a barn, factory, or warehouse are often completely dry to the core and the driest timbers available anywhere. It’s not easy to hand-scribe and connects irregular, twisted, and non-square reclaimed beams so the finished timber frame appears to have always been one frame.
We think a timber frame built from reclaimed wood is everything that today’s sleek, mass-produced, technology-saturated culture isn’t. It celebrates the cracks and character and dirt and all the other marks that time, weather, and use leave behind.
Interested in learning more about timber framing? Check out our timber frame blog.