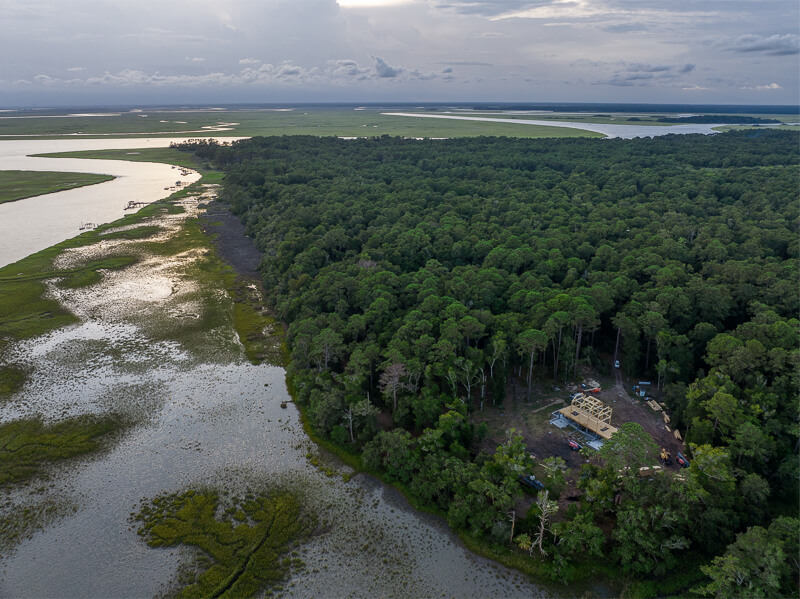
Building on an Island: What You Need to Know
Building a home on an island is a dream for many—but the logistics can quickly turn into a nightmare if you’re not prepared. From transporting materials by barge to dealing with unpredictable weather, island construction presents unique challenges. As a timber frame subcontractor specializing in complex builds, Carolina Timberworks recently completed an island project, and we’re sharing what we learned to help you plan your own remote build.
Why Building on an Island is Different Than the Mainland
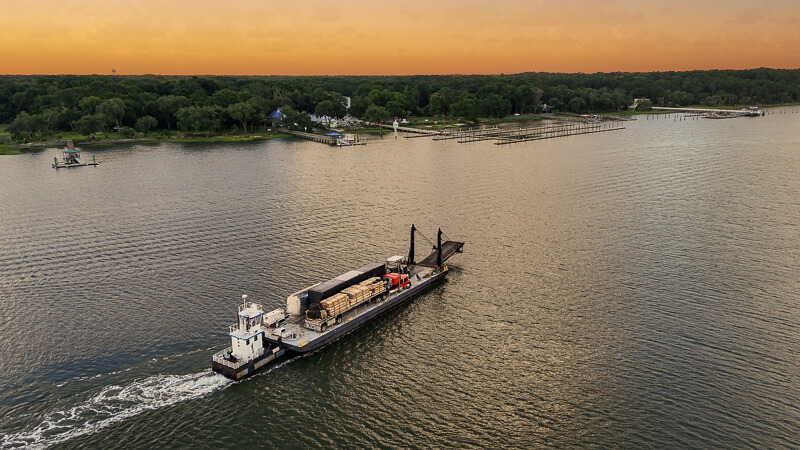
At first glance, building a home on an island may seem similar to any other construction project. But in reality, every aspect—from materials to labor to scheduling—requires a different level of planning. Here’s what makes timber frame construction uniquely challenging on an island:
1. Every Stick, Brick, and Person Arrives by Barge
On the mainland, materials roll right off a truck and onto the job site. On an island? Not so much. Every single piece—timbers, nails, tools, even lunch—must be carefully staged, loaded, and ferried across the water. That means no last-minute hardware store runs, no quick resupplies, and no margin for error. The logistics resemble a military operation, requiring precision, planning, and a team that understands the stakes.
2. Forget Something? Prepare for Costly Delays
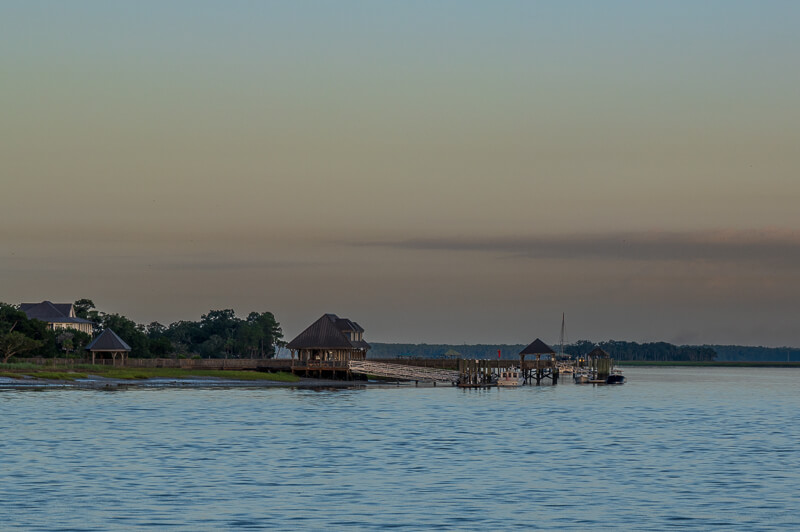
On a typical job site, a miscut timber or a forgotten handful of ¾” white oak pegs might cost you a day. On an island, that same mistake could set you back a week. There’s no quick trip to the supplier—every extra run across the water depends on barge schedules, tides, and availability, all of which are beyond your control. In remote construction, small problems don’t stay small for long.
3. Rain, Tides, and Isolation Demand Next-Level Logistics
On an island, nature calls the shots. Tides dictate when barges can run. Rain stalls work, but the crew is still on the clock. A passing storm can upend the schedule, while a broken-down barge can ripple delays across the entire project. It takes a certain mindset to thrive in conditions where predictability is a luxury.
4. Food and Lodging: More than Just a Place to Sleep
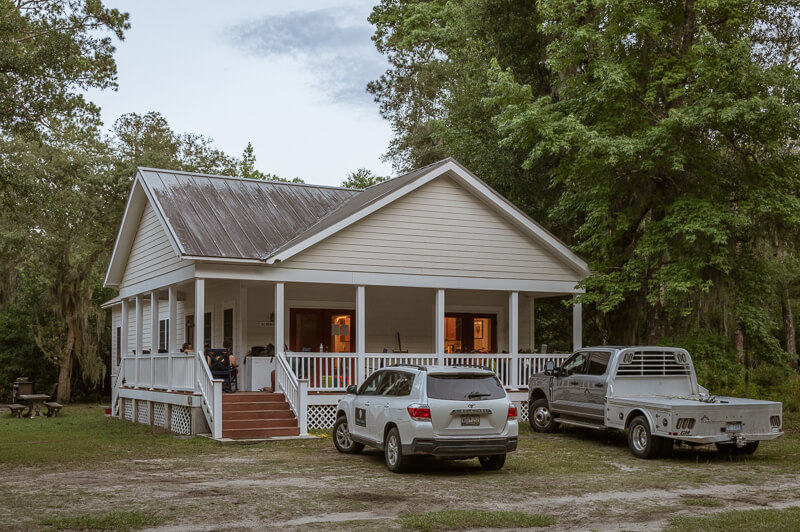
Getting materials across the water is only part of the challenge—you also have to get the crew there and make sure they’re taken care of. Lodging is rarely luxurious, but it needs to be comfortable enough for a team working long, physically demanding days.
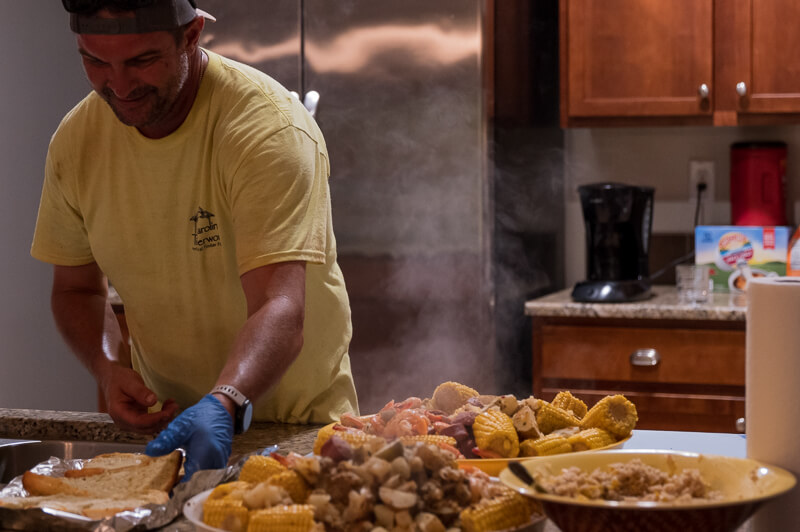
And then there’s food. When the nearest grocery store is miles (and a boat ride) away, you don’t just “grab something” after work. That’s where having a crew member like Tommy makes all the difference. A former restaurant owner, he took charge of meals—wearing gloves, using a thermometer, and treating dinner prep with the same level of care and precision as a timber frame layout. One night, he put together a classic Low Country boil—shrimp, potatoes, corn, and sausage—the kind of meal that makes the challenges of building in a remote location a little more enjoyable, and a lot more memorable.
Why Timber Frames Are Ideal for Island Homes
1. Speed: Faster Assembly, Less Time on Site
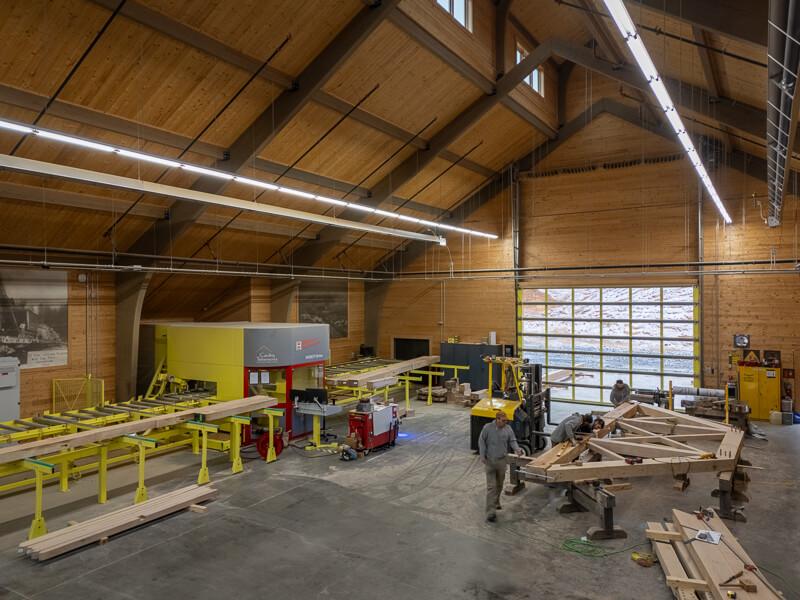
On an island, every extra day of construction adds logistical headaches and costs. Timber framing changes the equation. Instead of cutting and fitting each piece on-site, the entire structure is precision-cut in our shop using state-of-the-art CNC machinery. When the timbers arrive, they’re ready to go—slotted together like a giant puzzle by the same crew that fabricated them. What takes months with conventional framing can often be completed in weeks, minimizing time, risk, and weather exposure.
2. Strength: Built to Withstand Nature’s Fury
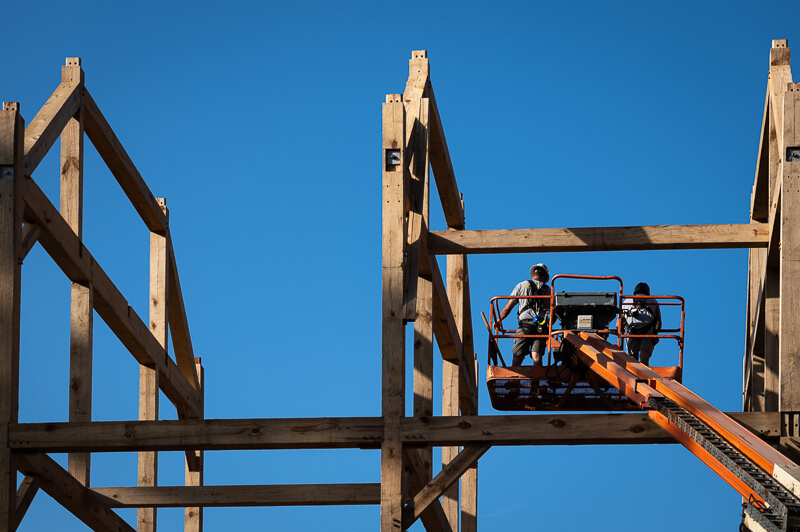
Island homes don’t just need to be beautiful—they need to be strong. Timber frames are engineered to handle the extreme: hurricane-force winds, heavy storms, and the relentless coastal climate. The interlocking joinery and massive timbers create a structure that is as durable as it is stunning, standing firm where lighter, conventionally framed homes might flex or fail.
3. Timelessness: Built to Last—and Loved for Generations
Timber framing isn’t a trend—it’s a building tradition that has been relied upon for over two thousand years. Long before mass-produced lumber and steel-framed glass boxes, people built with heavy timbers because they worked. These homes don’t just stand the test of time structurally; they endure because people love them. Timber-framed homes are cherished, maintained, and restored rather than torn down for something new. Their warmth, character, and craftsmanship make them worth preserving—whether on an island or anywhere else.
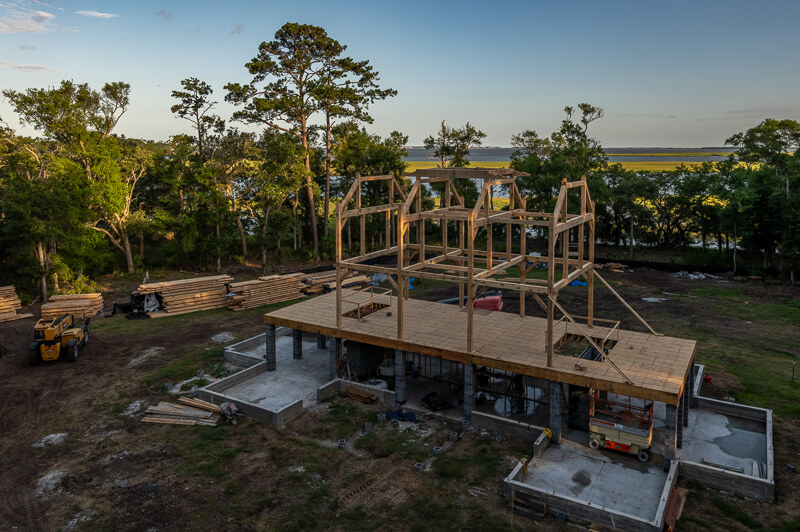
4. Less Waste, More Efficiency
On the mainland, construction waste is an afterthought—just toss it in the dumpster and schedule a pickup. On an island, every scrap of excess material has to be barged back off, turning waste disposal into a costly logistical challenge. Because we pre-cut every timber in our shop, there’s almost zero job-site waste. Fewer cutoffs, no piles of unusable material, and no need for expensive, hard-to-schedule dumpster hauls.
Considering Building on an Island? Here’s What to Know
Island construction isn’t for the faint of heart, but with the right team, it’s absolutely possible. If you’re considering a timber frame home in a remote location, the most important decision you’ll make is choosing experienced professionals who understand the unique challenges involved.
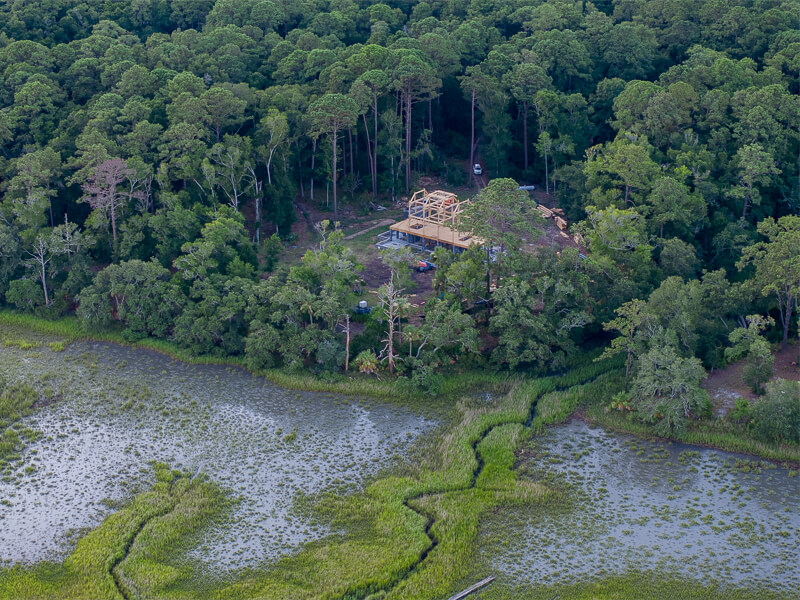
At Carolina Timberworks, we specialize in tackling complex builds—whether on an island, in the mountains, or anywhere that demands more than just the ordinary. Want to talk about your project? Get in touch with us.
Related
- A Primer on Timber Frame Construction
- Timber Frame Truss Ideas
- How to Interview a Timber Frame Company